This guide will provide a comprehensive overview of services provided by metal building contractors, ensuring you understand what to expect when hiring professionals for your construction project.
Key takeaways:
- Experience, licensing, and reputation matter when choosing a metal building contractor.
- Cost factors include materials, labor, customization, site preparation, permitting, and transportation.
- Metal building contractors can erect a variety of structures for different industries and purposes.
- Safety protocols are crucial for worker well-being and the integrity of the structure.
- Effective project management is key to a successful metal building project.
Criteria for Selecting a Metal Building Contractor
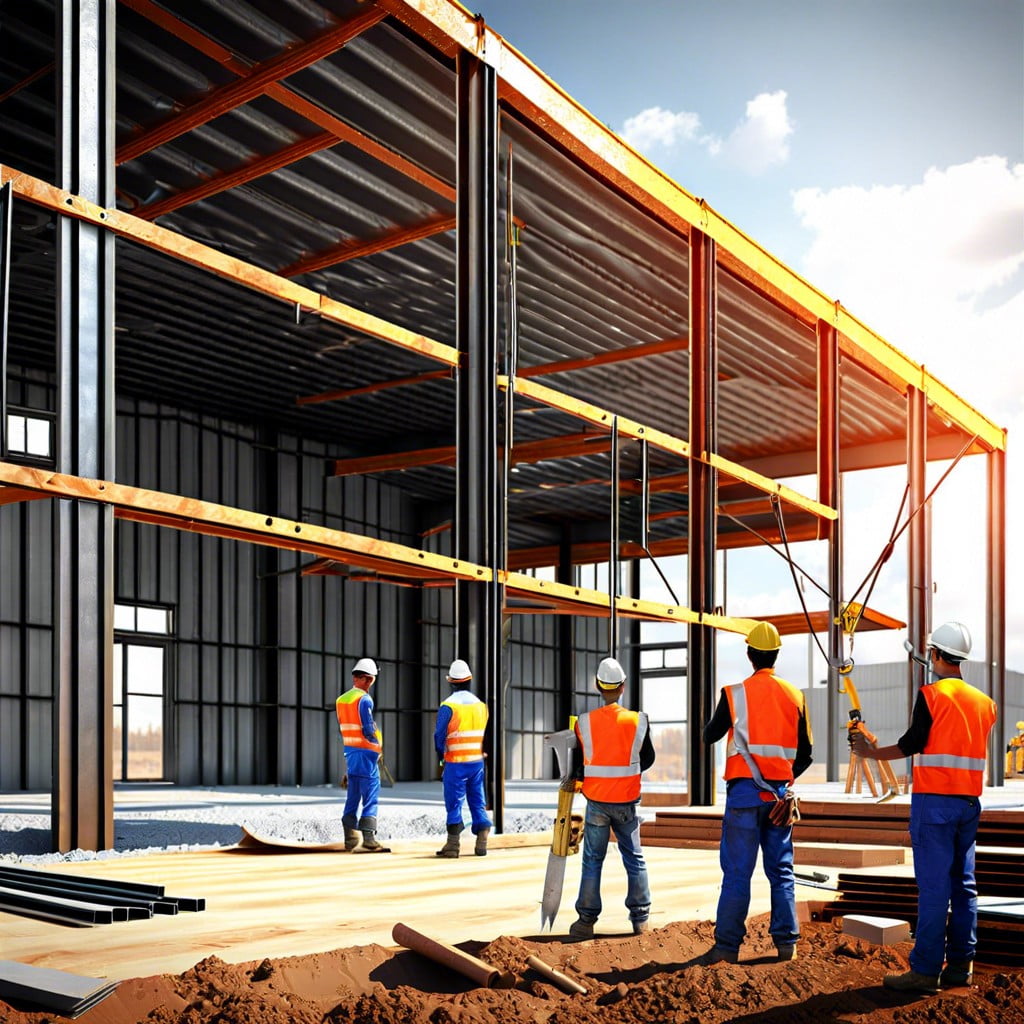
When choosing a metal building contractor, consider their experience and past projects. Those with a robust portfolio of completed buildings similar to your needs are likely to provide better results. Verify their licensing and insurance to ensure they meet state regulations and can protect you from liability.
Check references and reviews to gauge their reputation and the satisfaction of previous clients. A good track record is a strong indicator of reliable and quality service. Assess their expertise in local building codes and their ability to secure necessary permits, which is crucial for compliance and project timelines.
Inquire about their warranty and service policy. A contractor who stands behind their work will typically offer a substantial warranty and post-construction services.
Lastly, evaluate their communication skills. Effective communication throughout the project can greatly influence the outcome and your overall satisfaction. A contractor who listens to your needs and provides clear, timely updates is invaluable.
Metal Building Construction Cost Factors
Understanding the overall cost for metal building construction hinges on several key factors.
Material costs take precedence, as they can fluctuate based on market demand and the type of metal required—standard steel, galvanized steel, or aluminum varieties incur different expenses.
Labor costs are also significant. These are influenced by the complexity of the project, the skill level of the workforce, and prevailing wage rates in the area.
The customization of your building impacts the final price tag; the more complex the design, with added features such as insulation, specialized doors, or custom facades, the higher the costs.
Site preparation should not be overlooked. Factors such as ground leveling, foundation work, and accessibility can all alter the financial outlay of the construction phase.
Permitting and compliance with local building codes can have cost implications due to the administrative and materials standards that may need to be met.
Transportation of materials to the site can differ widely in cost, especially if the construction site is remote or requires specialized shipping methods.
The scale of the project plays a crucial role, as buying in bulk often means discounts on materials, but larger structures also require more labor and planning.
Remember, opting for a turnkey solution or working with a contractor who provides comprehensive services from design to completion can streamline the process and potentially reduce costs through efficiency and experience.
Types of Metal Buildings Erected By Contractors
Metal building contractors are adept at erecting a variety of structures tailored to specific industry needs and personal preferences. Agricultural buildings, often including large clear spans for machinery storage and livestock housing, are commonplace. Industrial facilities such as warehouses and factories prioritize functional space and load-bearing capacities. Commercial structures range from retail outlets to office buildings, designed with aesthetics and functionality in mind.
Residential metal buildings are also on the rise, with steel framing offering durability and design flexibility for homes. Aviation hangars, built with large doors and reinforced structures, house aircraft safely. Custom-designed buildings serve unique purposes, from recreation centers to church facilities, showcasing the versatility of metal construction.
Each type reflects an understanding of the distinct requirements inherent to its use—be it energy efficiency, sound insulation, or fire resistance. Contractors must combine architectural savvy with structural integrity to deliver buildings that meet both regulatory standards and client expectations.
The Importance of Safety Protocols in Metal Construction
Safety protocols are the backbone of any metal construction project. These guidelines ensure the well-being of workers and the integrity of the finished structure. A comprehensive safety plan includes regular training sessions, which equip the workforce with the knowledge to handle machinery correctly and to recognize potential hazards.
Personal protective equipment (PPE) is mandatory. Contractors must provide workers with safety gear, including helmets, gloves, and steel-toed boots, to mitigate the risk of accidents. Moreover, implementing fall protection systems such as safety nets and harnesses is crucial when operating at heights.
Regular equipment inspections are equally important. They help to catch any mechanical issues in construction machinery before they can lead to malfunctions or accidents.
In metal building construction, attention to fire safety can’t be overstated. Given that metalwork often involves welding and cutting, which generate sparks, having fire extinguishers and suppression systems on-site is necessary to promptly address any sudden outbreaks of fire.
Safety protocols also extend to the organization of the construction site. Clear signage and marked pathways keep the site navigable and help to reduce the likelihood of tripping or collision incidents.
In essence, diligent adherence to safety measures protects against delays and financial losses by reducing the number of work-related injuries and ensuring that projects remain compliant with local and federal regulations. It’s a fundamental aspect that reputable metal building contractors prioritize in their operations.
Project Management and Coordination
Effective project management is central to the successful completion of a metal building venture.
Experienced contractors designate a project manager to serve as the primary point of contact. This individual is tasked with overseeing all project facets, ensuring that each stage, from design to erection, adheres to strict timelines. They communicate regularly with stakeholders—clients, design teams, suppliers, and the construction crew—to coordinate the numerous activities that must occur in tandem.
Additionally, project managers utilize specialized software for scheduling and to track the project’s progress, mitigating potential delays. Budget oversight is also a crucial responsibility; they ensure that the project remains within financial constraints without compromising on quality.
Finally, project managers are skilled at troubleshooting. Should issues arise, their expertise in finding practical solutions minimizes downtime and keeps the project on course for timely completion. Through efficient coordination, they are the linchpin of ensuring that the finished metal building meets all specifications and quality standards.
Recap