Understanding the required thickness for a wall in plastic extrusion is crucial to ensure durability and structural integrity during construction.
The thickness of a wall for a plastic extrusion largely depends on the type of polymer used, the intended application, and the extrusion process itself. Generally, the wall thickness can range from 0.025 to 0.250 inches for standard extrusions. However, for more complex or specialized applications, it could be even thicker.
Ensuring the correct wall thickness is vital for the structural integrity and performance of the extruded product. In this article, we will delve into the factors that influence wall thickness, how to calculate it, and the considerations for different polymer types and extrusion processes.
Key takeaways:
- Wall thickness for plastic extrusion depends on polymer type and application.
- Uniform wall thickness ensures structural integrity and cooling consistency.
- Thicker walls are needed for heavy loads or intense wear.
- Thinner walls save materials but must maintain structural stability.
- Wall thickness tolerances depend on material choice and manufacturing process.
Understanding the Concept of Wall Thickness in Plastic Extrusion

Wall thickness in plastic extrusion refers to the measurement of the plastic’s sides once it has been shaped through the extrusion process. It’s a crucial variable to consider in plastic extrusion in ensuring structural integrity and functionality of the final product, depending on the specific use or application.
The thickness of the wall must be uniform all around for the extrudate to cool down evenly and maintain its shape when it solidifies. If the wall thickness isn’t consistent, areas of the plastic may cool quicker than others, leading to deformation or weak spots.
Design engineers keep a close eye on wall thickness during the extrusion process to prevent potential failures. The flexibility, strength, and durability of the extrudate are immensely influenced by its wall thickness.
A thicker wall for a plastic extrusion might be necessary if the final product is to bear a significant load or is expected to endure intense wear or stress. However, a balance must be struck to avoid excessive material usage, which can be cost-ineffective or result in unnecessarily heavy products.
Conversely, a thinner wall might suffice for products with fewer mechanical demands, leading to material savings. Still, designers must take care that the wall isn’t so thin that the product becomes frail or lacks structural stability.
It’s important to remember that specific wall thickness depends on the nature of the plastic being used, as different plastics have different strengths and attributes. Thus, understanding the properties of the chosen polymer is essential.
Note that while there are general guidelines and principles regarding wall thickness, they are not applicable universally. Each design will have its unique considerations based on end-use requirements, costing, and the specific polymers in use. Therefore, using simulation software or prototyping before full-scale production can be very beneficial.
Determining Adequate Wall Thickness for Plastic Extrusion
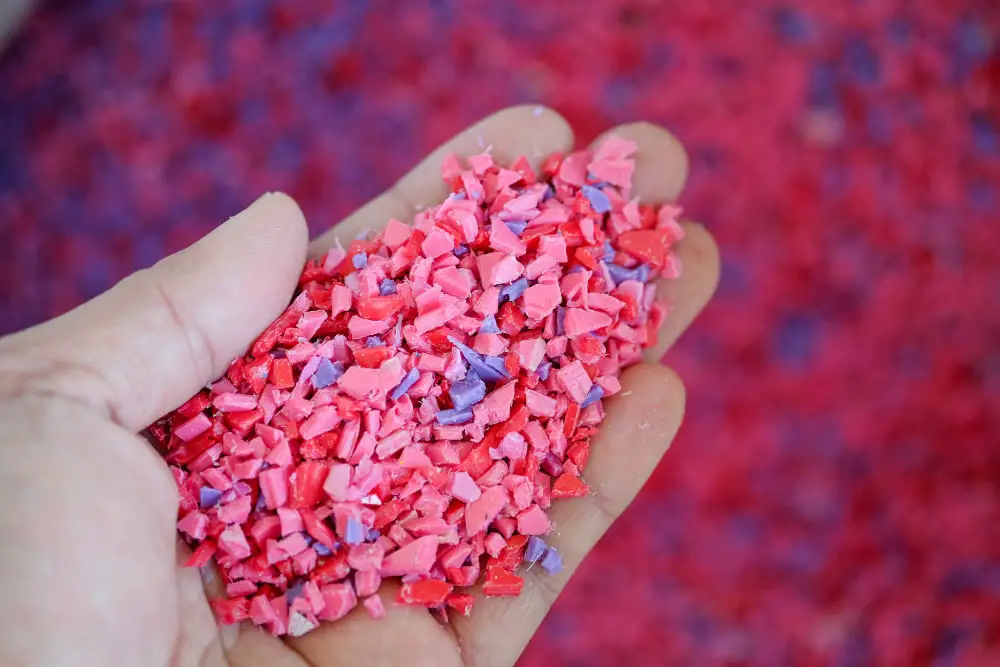
Wall thickness is an essential element to keep in mind when planning for plastic extrusion. Here are key considerations when determining the right thickness:
Different plastics respond differently to the extrusion process. Familiarising yourself with the plastic’s unique properties is vital. For instance, some plastics have a high shrinkage rate and require thicker walls to compensate.
The end-use of the plastic product also plays a pivotal role. If the extruded part is set to endure considerable stress or strain in its service life, a sturdier, thicker wall would be necessary.
Introducing regrind, i.e., recycled plastic, during extrusion can prompt for thicker wall requirements. Regrind can slightly degrade the plastic’s overall strength, hence a thicker wall compensates for this reduction.
The environment, where the extruded part will be used, may demand thicker walls. For example, a plastic pipe laid underground might require a thicker wall to withstand soil pressure or resist potential root penetration.
The extrusion speed is another factor worth considering. High-speed extrusion often leads to faster cooling and shrinkage, calling for a thicker wall to ensure the right dimensions post cooling.
Each of these considerations collectively informs the ideal wall thickness for each unique plastic extrusion project.
Role of Uniform Wall Thickness in Ensuring Quality Extrusion
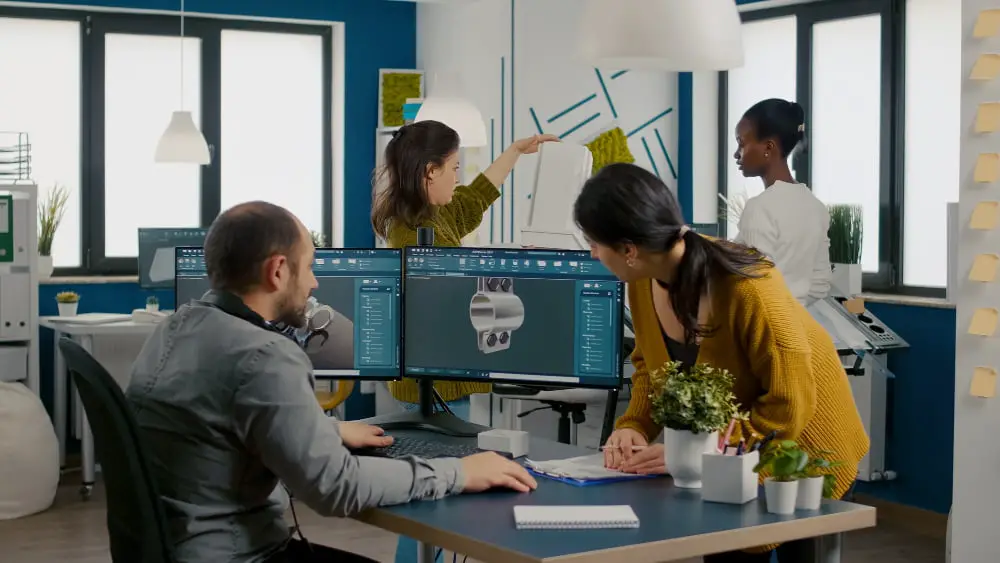
Maintaining a uniform wall thickness is a crucial factor in the quality of plastic extrusion. Let’s break it down:
- A uniform wall ensures consistent cooling and reduces warping. This is because the material cools from the outside in, leading to the outside skin forming first. If the wall thickness is inconsistent, the pieces of the polymer with more material will cool last, leading to deformations.
- It facilitates easier flow of the molten plastic during the extrusion process. If the wall thickness is not uniform, it can lead to an uneven flow rate which can cause defects in the finished product.
- It enhances the structural integrity of the product. Uniform wall thickness ensures the final product can withstand pressures evenly across its entire surface, reducing the risk of breakage or deformation under strain.
- Uniform wall thickness also helps in minimizing production errors such as sink marks. These marks can occur when the plastic shrinks around points of high wall thickness.
- To ensure uniform thickness, try using computer-aided design (CAD) software. This technology allows engineers to visualize the extrusion process in 3D and detect areas of different thickness before the manufacturing process begins.
- It’s also recommended to regularly inspect the wall thickness during the extrusion process. This helps in correcting inconsistencies as and when they occur.
Remember, keeping the wall thickness uniform might necessitate compromises in the design. However, it is one of the most practical ways of ensuring high-quality plastic extrusion.
Wall Thickness Considerations in Extrusion Corners
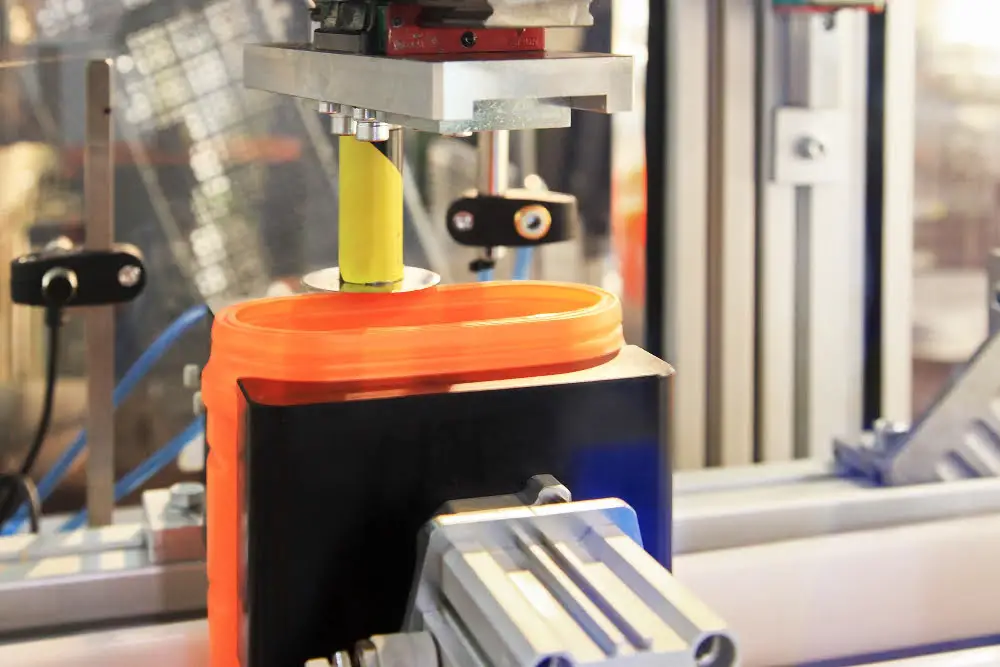
When shaping our corner sections during extrusion, we are cautious to avoid abrupt transitions and drastic variation, they can lead to flaws in your material post-production.
First, we round out the corners to ensure a smoother, continuous flow to the plastic. A circular or comma-like shape is easier for the molten plastic to navigate around.
Secondly, the inner radius of curves should not be less than half the wall thickness, if not, it might result in product failure.
Lastly, the preferred corner radius-to-wall thickness ratio is 0.5 to avoid sinking, increased stress concentration, and poor filling.
Adhering to these considerations ensures optimal product quality while maintaining structural integrity.
Understanding Wall Thickness Tolerances in Plastic Extrusion
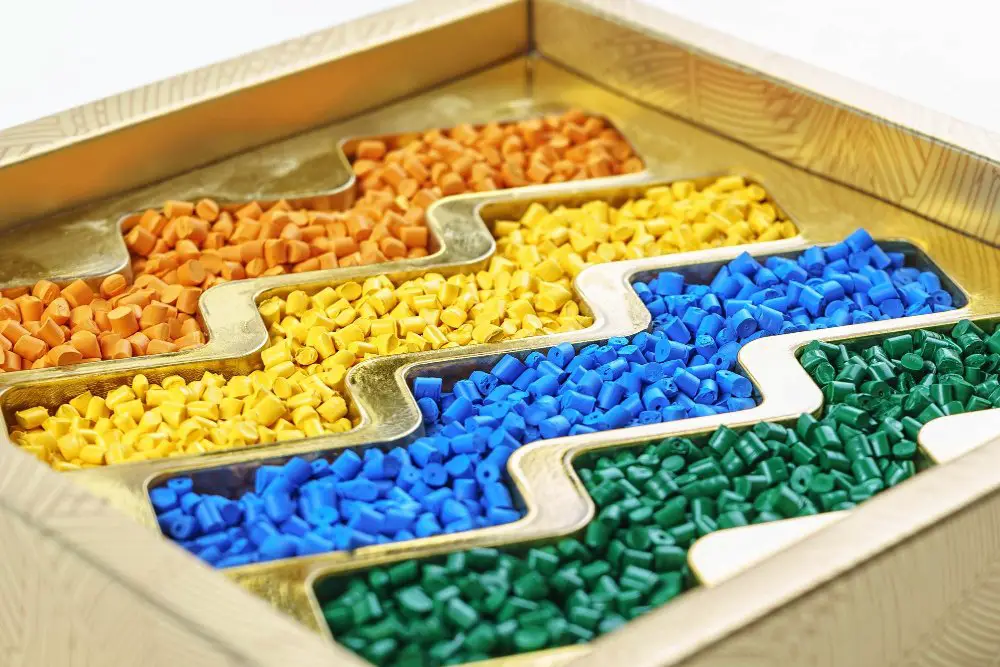
Tolerances in plastic extrusion refer to the allowable variations in wall thickness that do not impede the function, fit, or design of the product. While the ultimate goal in extrusion is to maintain uniform thickness, slight deviations are part of the process. Understanding these tolerances helps improve the design and manufacturing process, ensuring the final product meets quality standards.
Key Aspects of Wall Thickness Tolerances:
- Material Choice: Different polymer types have unique shrinkage rates. Taking these into consideration helps in achieving dimensional accuracy within set tolerances.
- Tool Precision: High-quality, well-maintained tools help maintain stricter tolerances.
- Manufacturing Process: Temperature control, feed rate, and cooling processes greatly affect dimensional tolerances.
- Design Complexity: More intricate designs are prone to higher variance in wall thickness. Incorporating draft angles and minimizing sharp corners can aid in managing tolerances effectively.
The key takeaway: when planning a plastic extrusion project, considering these factors during the design and manufacturing stages will greatly contribute to achieving desired wall thickness tolerances.
The Key Role of Wall Thickness in Plastic Extrusion Design
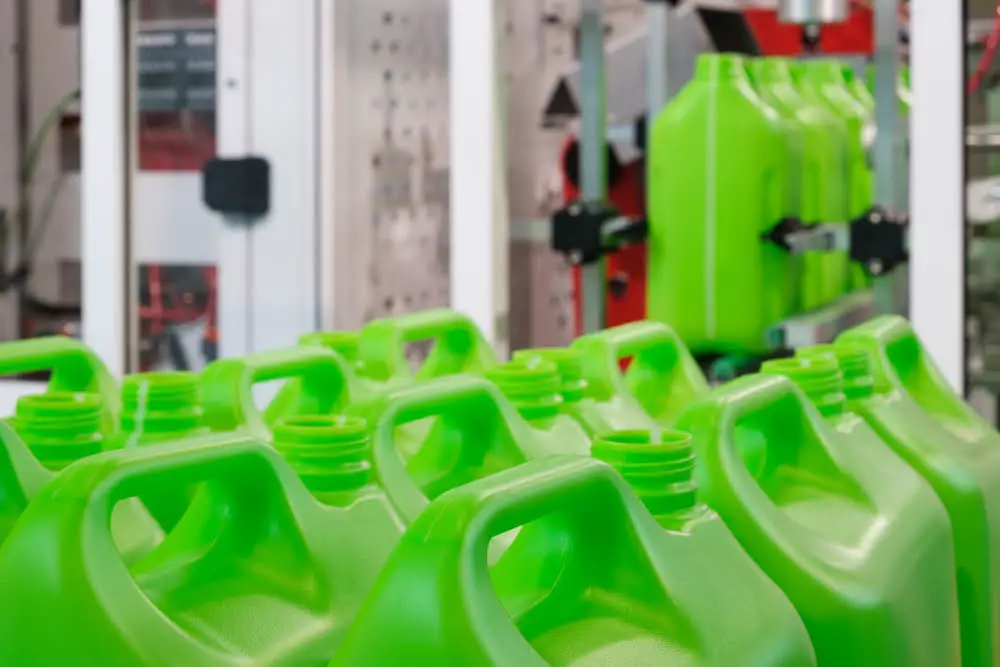
Maintaining the appropriate wall thickness in plastic extrusion design is a critical factor in the process. Each design might require a different thickness, depending on the end application.
Wall thickness directly impacts the quality of the final product. Too thick or too thin can lead to variability in performance and might impact the longevity of the product.
In addition, material flow rates during the extrusion process are heavily influenced by thickness. Uneven wall thickness can result in areas of low and high flow, creating an uneven product.
One major advantage is processing speed. Thin walls require less material, and consequently less time, to extrude. However, there’s a balance to strike. Walls that are too thin can result in structural issues or part failure.
To ensure optimal design:
- Uniform thickness is crucial. Avoid drastic changes in wall thickness, if possible.
- Design for the process. Keep in mind the workflow of the extrusion process during the design phase.
- Familiarize with your material. Different plastics behave differently, hence, understanding your chosen material can help dictate wall thickness.
These steps can ensure a successful and efficient plastic extrusion while maintaining high-quality results.
Guidelines and Resources for Engineers On Plastic Extrusion Wall Thickness
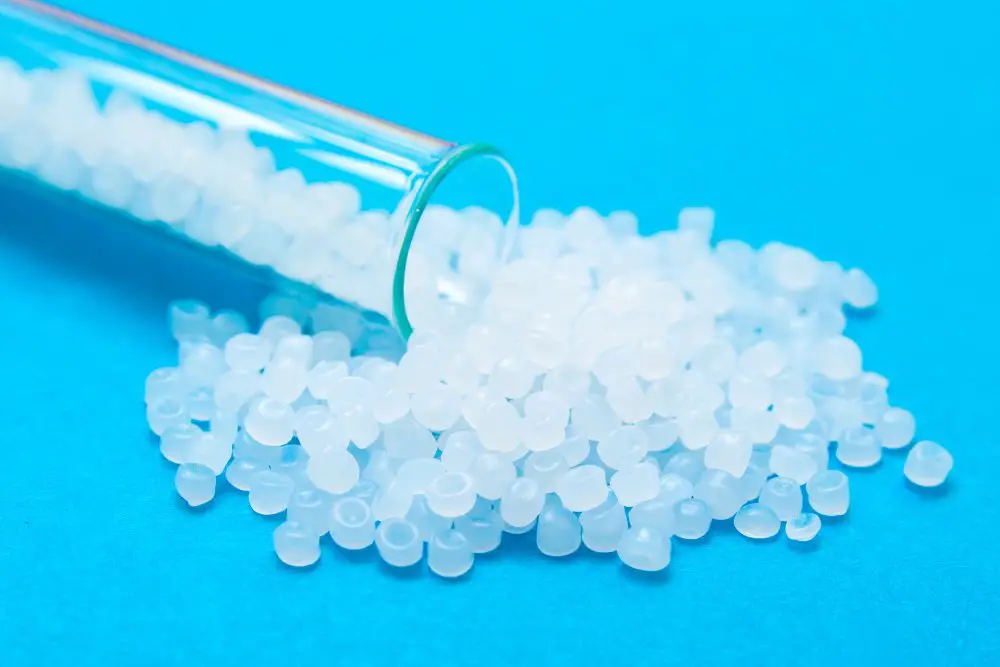
One key aspect engineers should consider when evaluating plastic extrusion wall thickness is the type of material being used. Different polymers possess unique flow and cooling characteristics that influence the optimal wall thickness.
Design of the extrusion also plays a major part. Complex designs may call for varied wall thicknesses to ensure structural integrity without sacrificing functionality.
Calculating appropriate thickness is aided by computer-aided design (CAD) software. This type of resource allows engineers to simulate and test the performance of different wall thicknesses before commencing actual production.
Paying attention to industry standards and regulations is equally important. These guidelines can provide engineers with acceptable ranges for wall thickness based on the type and purpose of the plastic extrusion.
Last but not least, real-world testing is essential to validate theoretical designs. Prototypes should be created and tested under practical conditions to confirm their durability and performance with the chosen wall thickness.
Remember, every extrusion project is unique and requires an individual assessment and adjustments to ensure all parameters, including wall thickness, are optimal.
FAQ
What is the thickness of extrusion?
The thickness of extrusion can vary from 1mm in the case of aluminium to 32mm for PVC.
What is the minimum radius for extrusion?
The minimum inside radius for extrusion is .010”, while the minimum outside corner radius is .020″.
What is the best plastic for extrusion?
The best plastic for extrusion is a commodity plastic, specifically polypropylene (PP), polyethylene (PE), or polyvinyl chloride (PVC) due to their availability, ease of processing, and cost-effectiveness.
Is plastic extrusion expensive?
Plastic extrusion is less expensive upfront due to lower tooling costs compared to injection molding, but becomes slightly more costly over time due to a higher medium cost per produced part.
What factors influence the optimal thickness of a plastic extrusion wall?
The optimal thickness of a plastic extrusion wall is influenced by factors including the type of polymer used, the desired product strength and flexibility, processing conditions such as temperature and pressure, and the product’s intended application.
How does the type of plastic material affect the extrusion process?
The type of plastic material massively impacts the extrusion process by determining factors such as the required temperature for processing, the cooling rate, and the final mechanical properties of the product.
Can the longevity and durability of a construction project be significantly affected by the characteristics of plastic extrusions used?
Yes, the characteristics of plastic extrusions can significantly affect the longevity and durability of a construction project due to their influence on the structural integrity and resistance capabilities of the built environment.
Recap