Understanding the cost of insulating a metal building is crucial because it impacts the budget, sustainability, and temperature regulation of your construction project.
Insulating a metal building is a smart investment that significantly cuts down on energy costs and enhances comfort. The cost of insulating a metal building varies widely, depending on factors such as the size of the building, the type of insulation used, and the labor costs in your region.
Typically, you can expect to spend between $0.50 to $2.00 per square foot for materials alone. This article dives deeper into the costs associated with insulating a metal building, providing a comprehensive breakdown of expenses and factors that can influence the final price.
Read on to gain a detailed understanding of what to expect when budgeting for this crucial part of metal building construction.
Key takeaways:
- Cost of insulating a metal building varies widely, ranging from .50 to .00 per square foot for materials alone.
- Types of insulation for metal buildings include blanket insulation, spray foam insulation, rigid board insulation, and reflective foil insulation.
- Factors to consider when insulating a metal building include climate, building size, intended use, and energy efficiency.
- Spray foam insulation is priced per square foot, with open-cell foam costing .44 to .65 per board foot and closed-cell foam ranging from .00 to .50 per board foot.
- Insulating a metal building provides benefits such as reducing heat transfer, decreasing energy bills, preventing condensation, and improving comfort.
Types of Insulation for a Metal Building: Comparing Costs and Benefits
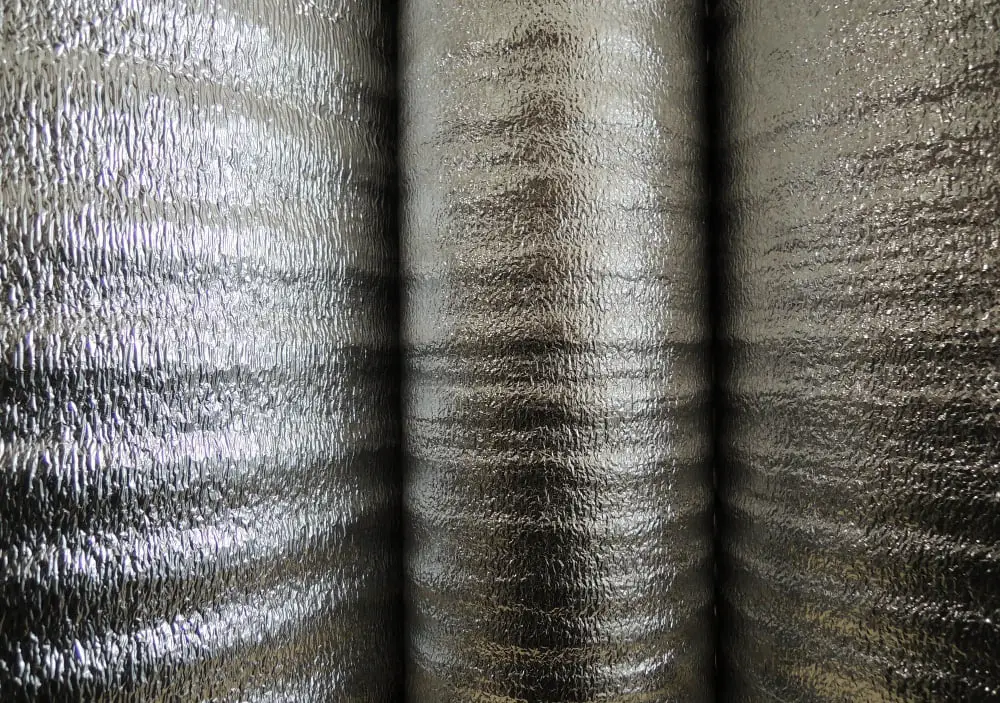
To adequately insulate your metal building, you can choose from various options, each with distinct costs and benefits.
Blanket insulation, popular due to affordability and ease of installation, could be an ideal choice if you’re on a budget. It provides a standard level of energy efficiency and is perfect for moderate climates.
Spray foam insulation excels at filling gaps and cracks, ensuring a higher degree of air-tightness compared to blanket insulation. Though pricier, its superior thermal performance and ability to hinder moisture intrusion can offer long-term savings.
Rigid board insulation provides excellent thermal resistance and stability, often used in commercial buildings. However, its costs can be higher compared to other insulation types due to its complex installation.
Reflective foil insulation is best suited to hot climates. Using reflective technology, it bounces off radiant heat from the sun, keeping the building cool. Its lightweight nature and easy installation make it an attractive option, albeit less effective in colder climates.
While each insulation type has unique advantages, it’s crucial to consider the specifics of your property and climate to make the best decision.
Factors to Consider Before Insulating A Metal Building: Climate and Building Size
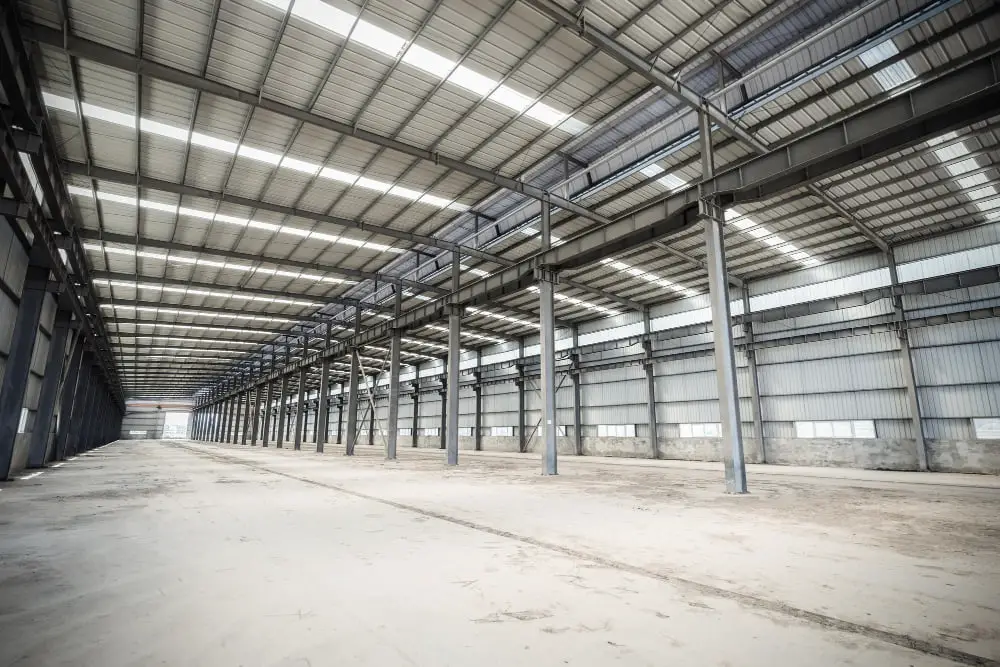
Analyzing your area’s climate is critical in determining the appropriate insulation method for your metal building. Coastal regions experience humid climates and need vapor resistant insulation to prevent rusting. On the other hand, buildings in cooler climates require higher R-value insulation to maintain heat.
The size of the building also plays an instrumental role. Larger buildings necessitate more insulation materials, consequently increasing the overall cost. Additionally, the design complexity matters; buildings with offsets and corners might cost more to insulate than those with a simple rectangular design.
Understanding these basics can guide you in making informed decisions, thereby maximizing your initial investment in insulation.
Factors to Consider Before Insulating A Metal Building: Intended Use and Energy Efficiency
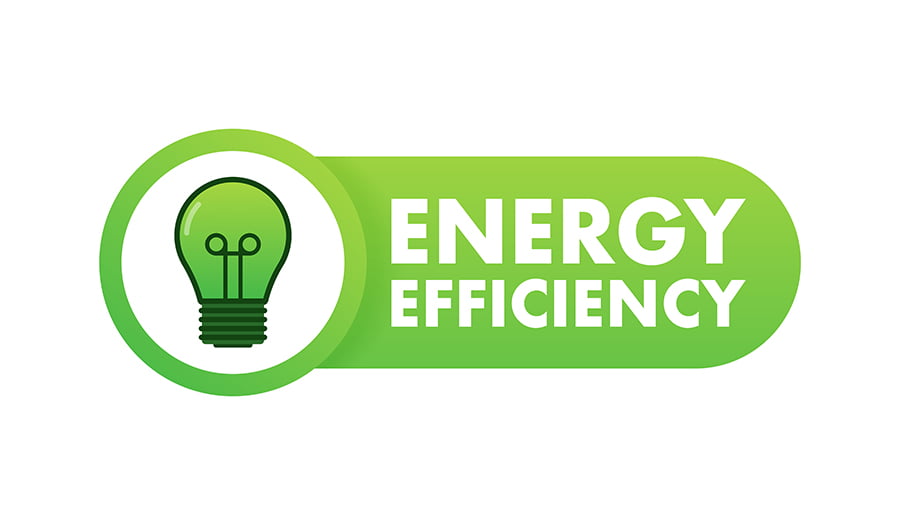
Optimizing insulation according to the building’s purpose could lead to significant energy savings over time. In residential or commercial settings, where heating and cooling systems are frequently used, a higher insulation value may be necessary. Conversely, structures used primarily for storage may require a less intensive insulation approach, thereby saving initial costs. Understanding this will inform better choices on the type and amount of insulation needed.
Energy efficiency is another paramount aspect. Proper insulation greatly reduces energy consumption by maintaining a consistent indoor temperature, irrespective of the external weather conditions. Installing adequate insulation can henceforth reduce utility costs, and simultaneously contribute to environmental sustainability. It is advisable to assess the long-term energy savings against the upfront cost of the insulation to ensure the return investment is worthwhile.
Cost Analysis: Metal Building Spray Foam Insulation
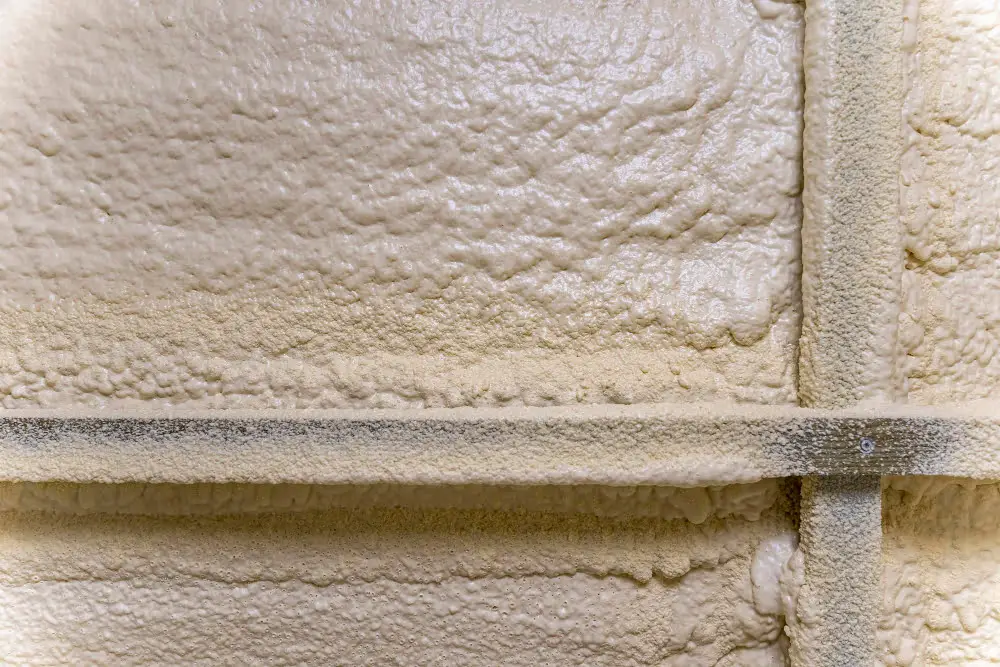
In terms of cost, spray foam is typically priced per square foot, with the exact rate varying based on thickness and type – open-cell or closed-cell foam. On average, open-cell foam costs around $0.44 to $0.65 per board foot, while closed-cell foam tends to be pricier, ranging from $1.00 to $1.50 per board foot.
Keep in mind that these are approximate figures, and prices can fluctuate based on local market conditions or installation complexities. Annual maintenance or replacement costs are usually minimal to nonexistent, resulting in significant long-term savings.
Despite its higher upfront cost, spray foam insulation offers unparalleled energy efficiency benefits. With superior capacity to seal crevices and corners, it significantly cuts down energy consumption, translating into noticeable reductions in heating and cooling bills. These savings should be factored into the overall cost analysis.
While the more inexpensive open-cell foam offers moderate insulation performance, the closed-cell variant boasts higher R-value – a measure of thermal resistance – providing superior insulation and moisture control. Therefore, the choice between open-cell and closed-cell foam largely hinges upon the specific insulation requirements of your metal building and your budget allocation.
Benefits of Insulating a Metal Building: Heat and Cold Transfer Reduction
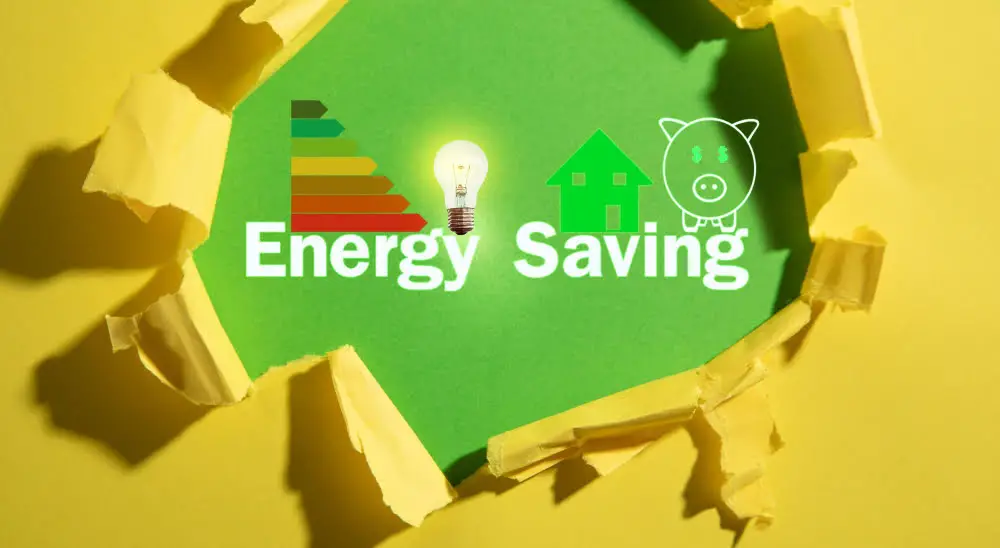
Proper insulation serves as a formidable barrier between the interior of a metal building and outside weather conditions.
1. Mitigating Heat Transfer: During the warmer months, insulation assists in reducing the amount of heat absorbed by the metal building. This helps to maintain a cooler internal environment, promoting comfort and energy efficiency.
2. Decreasing Cold Transfer: In colder weather, the insulation works in reverse. Rather than letting the indoor heat escape through the metal walls and roof, it forms a shield, retaining warmth and substantially decreasing the reliance on heating systems.
3. Reduction in Energy Bills: With a balanced indoor temperature, less strain is placed on climate control devices such as air conditioners and heaters. This translates into significant energy saving and lower utility bills.
Remember, while every metal building is unique in its shape and size, the fundamental principles of heat and cold transfer and their reduction through insulation remain the same. This makes insulation and energy efficiency crucial considerations for your metal building project.
Benefits of Insulating a Metal Building: Prevention of Condensation
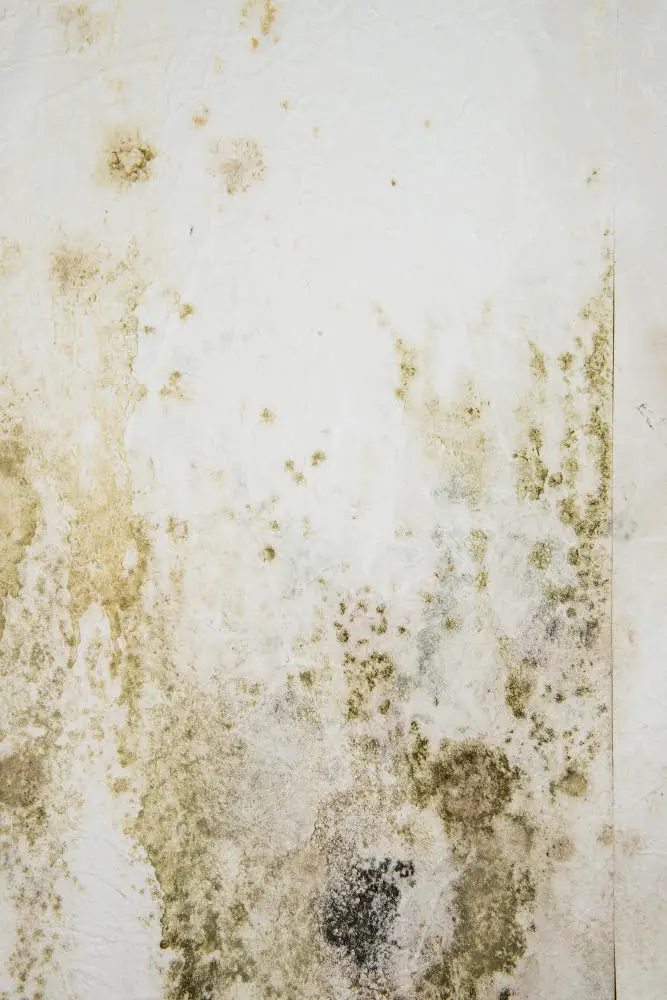
Considerable value is found in preventing condensation within your metal building, primarily due to the negative impacts moisture can have on both the structure and interior goods. When metal surfaces encounter warm, humid air, it can result in water droplets forming on the surface, which is a process known as condensation. This could lead to detrimental effects including rust, mold and mildew.
Insulation acts as a protective barrier against moisture collections, effectively eliminating these risks. Quality insulation also allows for the avoidance of any potential damage that might be caused by dripping water, preserving the durability and longevity of your interior environment and stored items.
Moreover, a properly insulated building ensures a comfortable, dry atmosphere, fostering an overall better experience for those operating within the structure. This can be especially crucial for metal buildings used as workshops, garages, or any form of human habitation.
Finding the Most Cost-Effective Way to Insulate a Metal Building
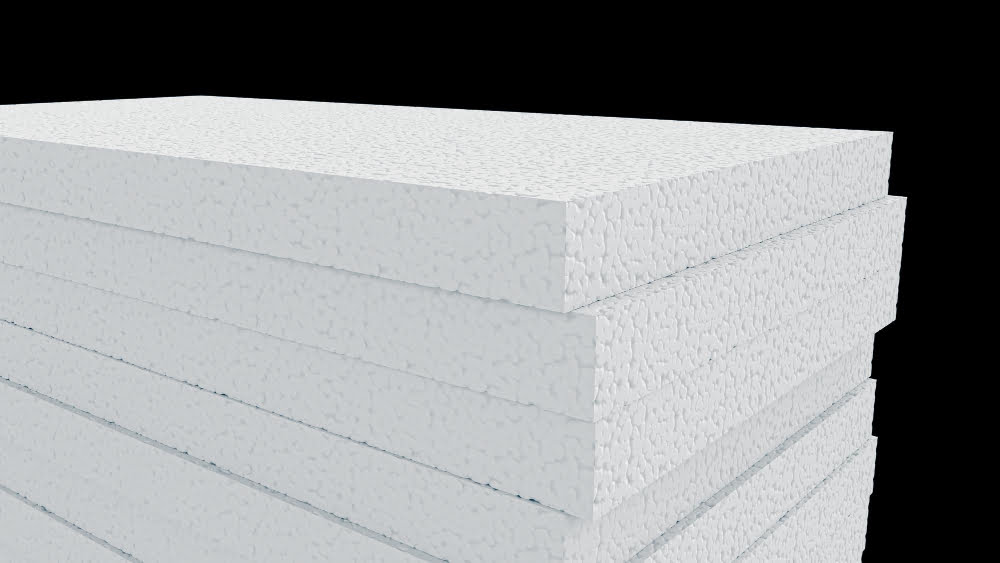
Taking into account monetary considerations, finding the best balance between the cost of the insulation material and the long-term utility savings it will yield is pivotal. Several possibilities are worth exploring:
1. Bulk-fill insulation is generally cheaper than spray foam alternatives, and offers decent thermal protection making it a value choice.
2. Reflective foil—typically used in conjunction with other insulation—is low in cost and effective at preventing radiant heat transfer.
3. Rigid board insulation, although more pricy initially, offers superior thermal resistance in minimal space and can contribute towards long-term energy saving.
Lastly, considering professional installation versus DIY methods is crucial. A professional service might be more expensive upfront, but incorrect or inadequate installation could compromise insulation effectiveness, leading to potential loss in energy savings.
FAQ
Is it worth insulating a metal building?
Yes, insulating a metal building is worth it as it regulates heat flow, prevents condensation, manages noise levels, and can boost lighting efficiency, alongside maintaining internal heat during winters.
What is the cheapest way to insulate a metal building?
The cheapest way to insulate a metal building is through fiberglass batt insulation, which is cost-effective, widely available, and easy to install.
Can you insulate a metal building after it’s built?
Yes, a metal building can be insulated after it’s built by using refacing insulation materials or adding a new layer of fiberglass with new facing materials attached.
What is best to insulate a metal building?
The best way to insulate a metal building is by utilizing a fiberglass insulation system that comes with a vapor retarder to reduce the amount of water vapor entering the building.
How does the size of a metal building influence the insulation cost?
The size of a metal building directly influences the insulation cost as larger buildings require more insulation materials, thereby increasing the overall cost.
What types of insulation are recommended for metal buildings and how do their costs compare?
The commonly recommended types of insulation for metal buildings are fiberglass, spray foam, and rigid foam, with fiberglass being the most cost-effective, followed by rigid foam, and spray foam usually being the most expensive.
How does climate impact insulation needs and costs for a metal building?
Climate significantly impacts insulation needs and costs for a metal building due to differences in heat transfer and condensation risks that vary with geographical location.
Recap