Exploring the various factors that determine the cost of a metal building can provide valuable insights for anyone interested in this durable and versatile construction option.
Determining the cost of a metal building involves several factors such as the size, design, and customization options. On average, the price can range from $16 to $20 per square foot for basic structures, and for more complex or customized buildings, the cost can go up to $40 per square foot.
However, these are just ballpark figures. To get a more accurate estimate, it’s important to consider the specifics of your project. In this article, we’ll delve into the different components that influence the final cost of a metal building, providing you with a comprehensive understanding of where your money goes.
Key takeaways:
- Metal building costs range from to per square foot.
- Factors that affect costs include size, design, location, and materials.
- Customization options like size, architecture, and materials increase costs.
- Prefabricated steel buildings are more cost-effective than custom-engineered.
- Costs for residential, agricultural, and commercial buildings vary.
Factors That Affect Metal Building Prices
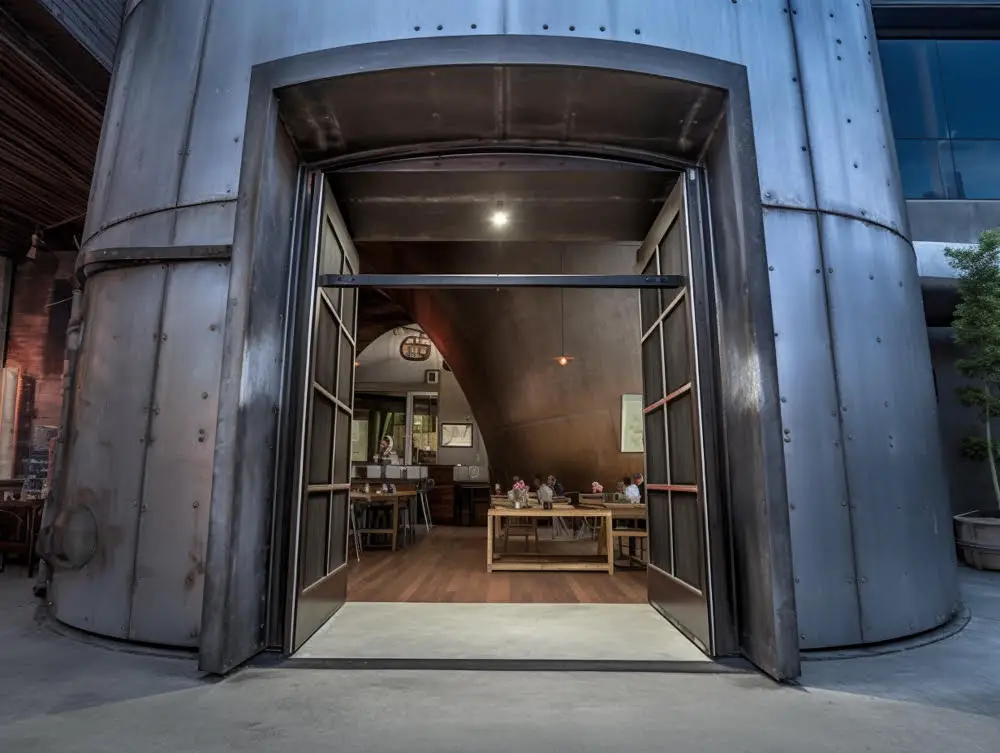
When considering costs, several factors come into play with metal structures.
First, the building’s size is paramount; larger structures typically mean more materials and higher costs.
Next, the design complexity influences cost. Simple, regular shapes are less expensive as they require less tailor-fit components compared to unusual or complex designs.
Furthermore, the site’s location plays a role, as installation in challenging terrains may raise costs due to extra work or special equipment needed for ideal placement.
The building’s purpose also has a dramatic effect on costs—whether it’s for residential, agricultural, or commercial use, each use comes with specific building regulations that may impact cost.
Finally, the choice and quality of materials determine financial outlay. Higher-grade, more robust, and durable materials are pricier, but they offer an extended lifespan of the building.
Being aware of these factors will help you manage and plan your capital around your metal building project, providing a more accurate budget forecast and potentially highlighting areas for cost-saving opportunities.
Design and Customization Considerations for Metal Buildings
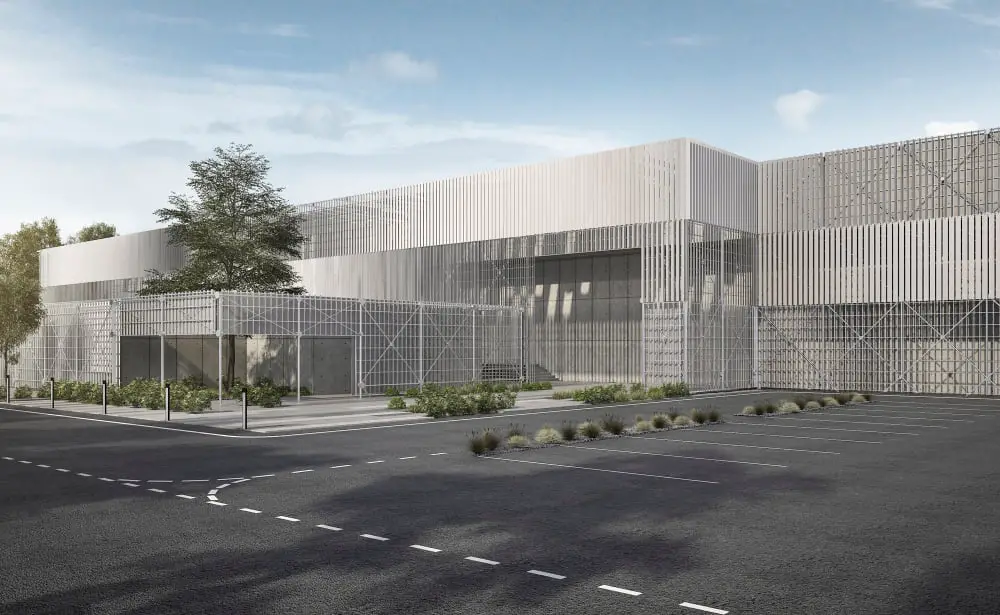
Customization plays an integral role when determining the cost of a metal building. The simple fact is, the more complex and personalized your structure, the higher the price.
1. Specific Size Requirements: Buildings designed to fit non-standard dimensions will add to the overall cost. Uniquely sized parts require additional engineering and fabrication work.
2. Unique Architecture: Custom architectural details such as unconventional roof styles, intricate trusses, or specific window placements all add to the base price.
3. Specialized Materials: Opting for high-end finishes, premium insulation, or specialty doors and windows not only improve the aesthetic and utility value of your metal building but will also affect the price.
4. Exterior Enhancements: Any enhancements such as brick, stone, stucco or wood paneling done to the building’s exterior, to make it blend with the surrounding properties, will also reflect on your bill.
5. Interior Layout: Custom interior layouts including partition walls, added rooms, or features like mezzanine floors will necessitate extra materials and labor, thus raising the cost.
6. Certifications and Codes: Depending on the building’s purpose, there may be local regulations or certifications required which may affect the design, engineering, and materials used, affecting the overall costs.
Therefore, it’s essential to have a well-planned design with cost-effective customization choices to strike a balance between functionality and budget.
Your Construction Choices: Price Implications
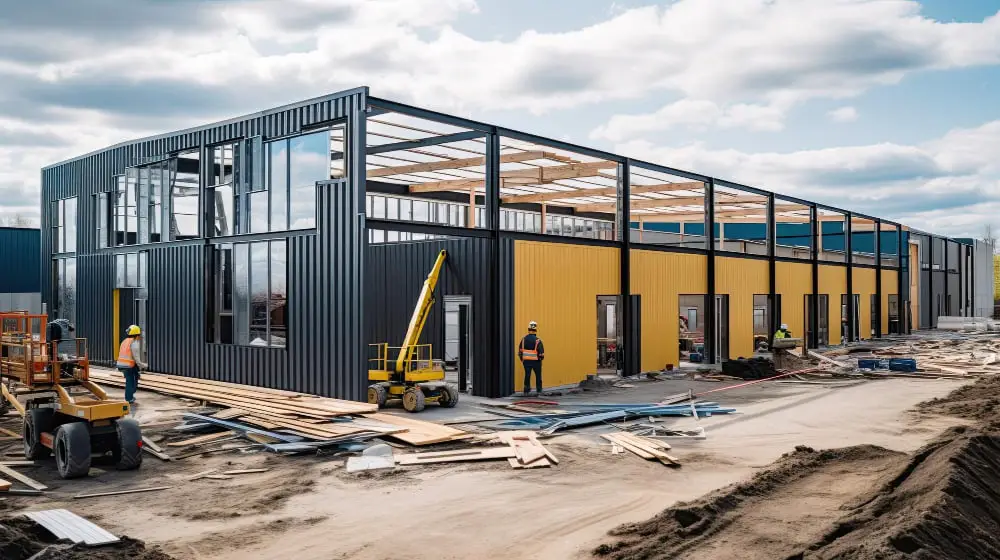
Selecting the right construction method can largely influence the final cost of your metal building. Primarily, there are two types of construction choices – prefabricated steel buildings and custom-engineered buildings.
Prefabricated or “prefab” buildings are cost-effective as they are manufactured in bulk, pre-cut and pre-drilled, saving labor time and factory processing costs. However, they come with limited customization options and may not suit complex requirements.
On the other hand, custom-engineered buildings cater to your specific design requirements. These buildings, while offering flexibility and uniqueness, can significantly bump up the overall cost. This is due to the additional work involved in custom designing, engineering, and fabrication.
If you are working on a tight budget, consider mixing and matching both concepts. Opt for prefab for structural elements and invest in custom-designed elements for unique features where necessary. Remember, the best choice always depends upon your specific needs, budget, and the overall project goals.
Average Cost for Residential Metal Building
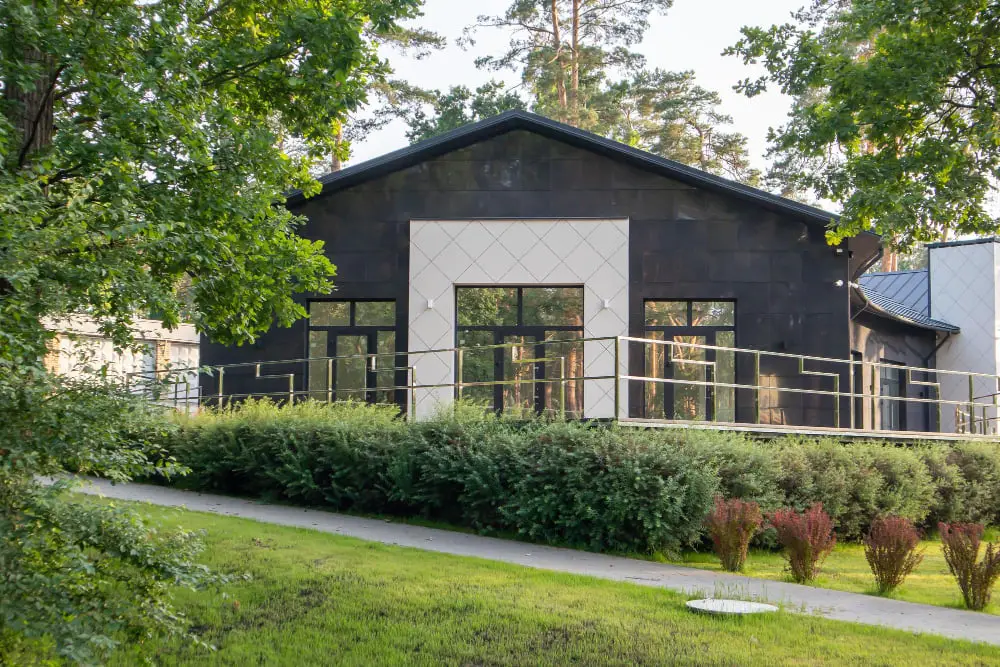
Though prices fluctuate depending on an array of factors, the average cost for a residential metal building usually falls within a range of $20-$40 per square foot. This estimation includes both the material and labor costs.
1. Size: Larger structures tend to have a lower cost per square foot, as materials can be purchased in bulk.
2. Customizations: Extra features such as wider doors, insulation, or specialty finishes can increase costs.
3. Level of Complexity: More complex designs, incorporating arched roofs or multilevel flooring, can add to the overall cost.
4. Site preparation: Adding in the cost of land level, the necessary foundation work, and all potential impact or zoning fees should be considered.
5. Labor Cost: Extent of manual labor, skill level, and local average wage rates are also essential for determining the final price.
Take these into account while planning your own residential metal building project to get a more accurate cost prediction.
Average Cost for Agricultural Metal Building
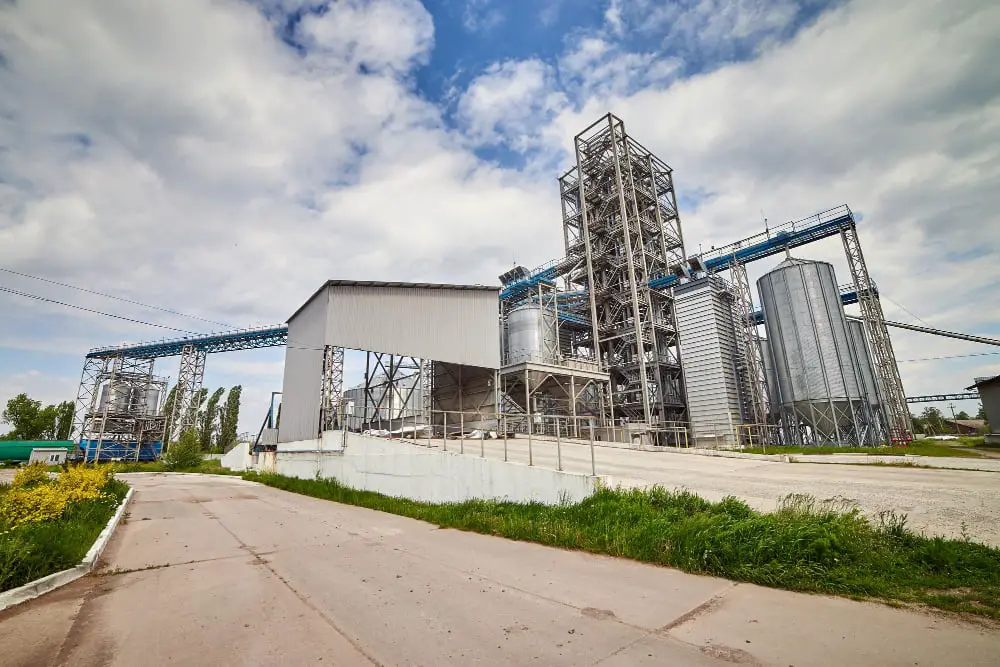
Breaking down the cost components, the average price of agricultural metal buildings usually ranges between $50,000 to $115,000, with the price per square foot varying between $16 to $20. This range, however, significantly depends on the specific needs, customizations, and complexity of the design.
Three main factors typically drive the overall cost:
- Size: A bigger building will naturally cost more. Still, the price per square foot may decrease with the increase in size due to economies of scale.
- Manufacture & Installation: Costs can swing based on whether you select a pre-manufactured building or opt for onsite fabrication. The technical demands and time investment for installation also impact the budget.
- Customizations: Unique features or requirements such as temperature control, insulation, and additional fixtures could significantly raise the price.
Remember, staying informed on these components can aid in tailoring your project to fit within a realistic budget.
Average Cost for Commercial Metal Building
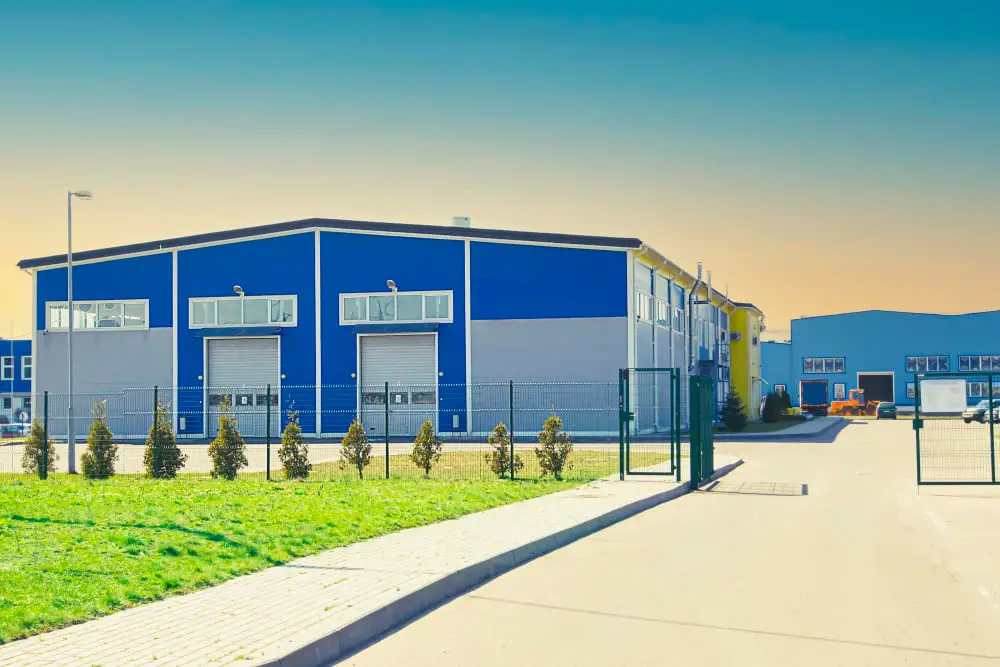
Commercial metal buildings are a go-to choice for many businesses due to their versatility, durability, and cost-effectiveness. And yes, they differ in price based on size and features.
For instance:
- Basic structures, referred to as rigid frame buildings, with dimensions like 30×40, can range from $9,000 to $11,000, prior to any customizations.
Average-sized commercial structures, such as 50×100 to 60×100 feet, typically run anywhere from $30,000 to $50,000.
For very large commercial buildings, like warehouses or distribution centers, the price can exceed $100,000, especially when adding features like insulated walls, doors, or customized facades.
Remember, these costs are estimates and can vary based on design complexity, local building regulations, site preparation, and the current price of steel. Furthermore, the more you tailor your building to specific needs or aesthetic preferences, the greater impact on cost. But fear not, this initial investment often equates to significant savings over time, given the reduced need for maintenance and repairs compared to traditional construction.
Average Square Foot Cost By Steel Building Size
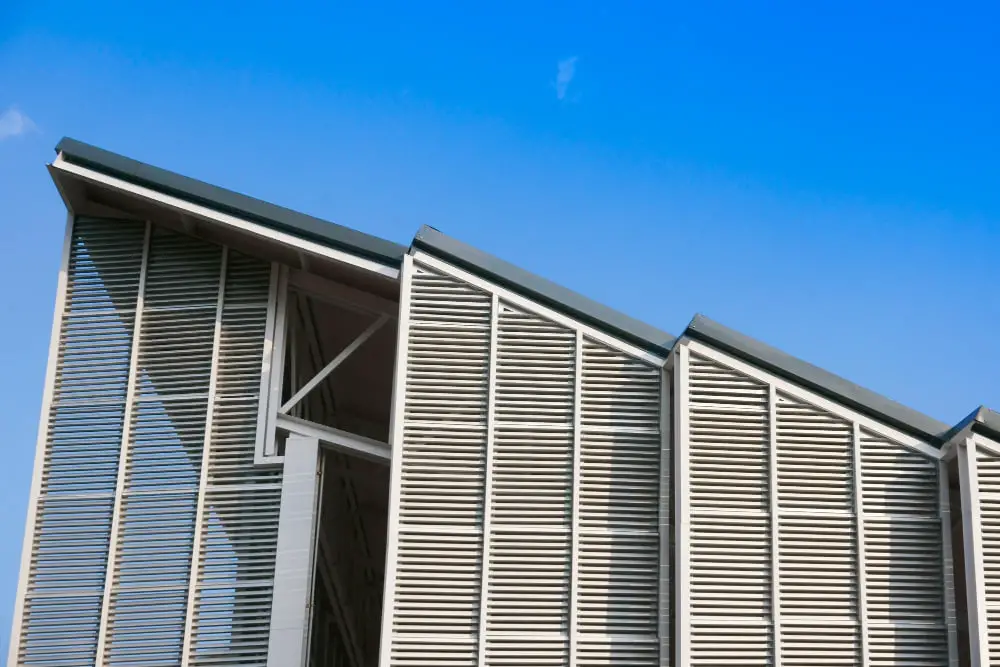
Square footage directly impacts the cost of a steel building. Smaller structures, like sheds or workshops, that range from 100 to 500 square feet, may cost between $5 and $20 per square foot. Buildings between 1000 and 2500 square feet, often used as garages, fall within a price range of $7 to $30 per square foot.
For larger facilities, like warehouses and industrial buildings ranging from 5000 to 10000 square feet, costs can be between $15 and $35 per square foot. These prices generally include both the material cost and labour, but it’s important to note that factors such as internal customization, installation complexity, and local regulations can increase these amounts.
The cost per square foot tends to decrease as the building size increases, offering economies of scale. This is primarily because certain fixed costs, like design and machinery, are spread out over a larger area, bringing down the cost per unit area.
Consider, too, how future expansion may influence costs. Planning for this in advance can prove more cost-effective than having to modify the building later on. It’s essential to balance immediate needs with potential future requirements to achieve the most economical and practical construction solution.
Metal Building Cost Calculator
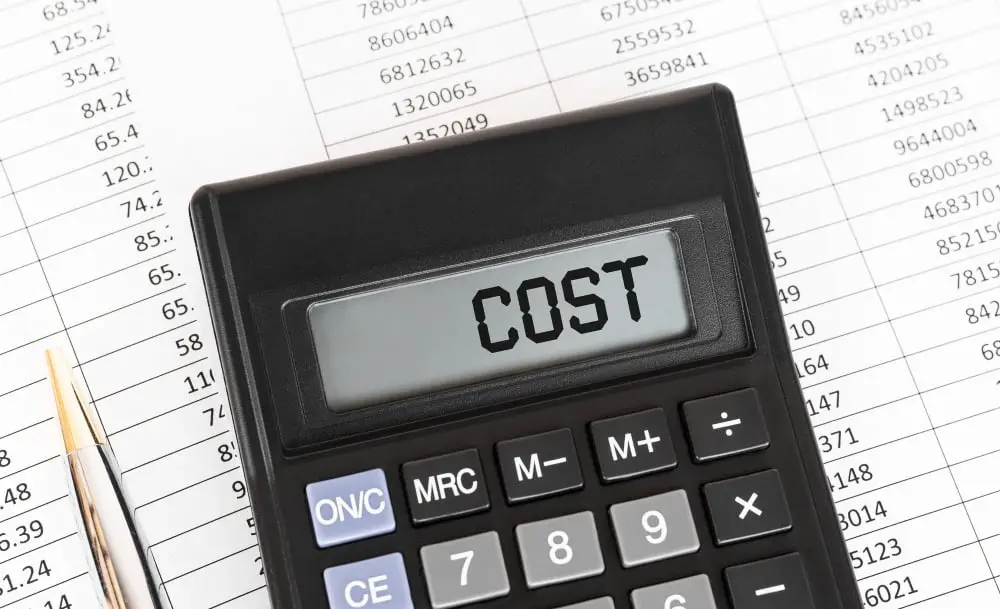
Utilizing a metal building cost calculator can provide a more personalized cost assessment. These interactive tools are generally found on suppliers’ websites and require input data to generate an estimate. Key information you’ll typically need to enter includes building size, design, location, and any additional features or customizations.
Calculating on the base of size is rather straightforward: the larger the construction, the higher the costs will generally be due to increased material amounts and required labor. Design features such as wall height, roof style, windows, doors, and insulation can also significantly affect cost, with more complex or high-quality options commanding higher prices.
The building’s location comes into play as shipping costs for materials can vary depending on distance to site and ease of access. Certain geographical areas may also have zoning rules or building regulations impacting construction and thus reflecting in the fee.
Extra features or customization – such as interior finishing, additional insulation, or specialized doors and windows – can also add to the final bill. These elements are often optional, so careful consideration of your needs vs. wants can help keep costs in check.
While a cost calculator provides an indicative estimate, it’s worth noting that actual costs may vary. Seek quotes from multiple suppliers for a more accurate comparison.
How to Save Money On a Metal Building
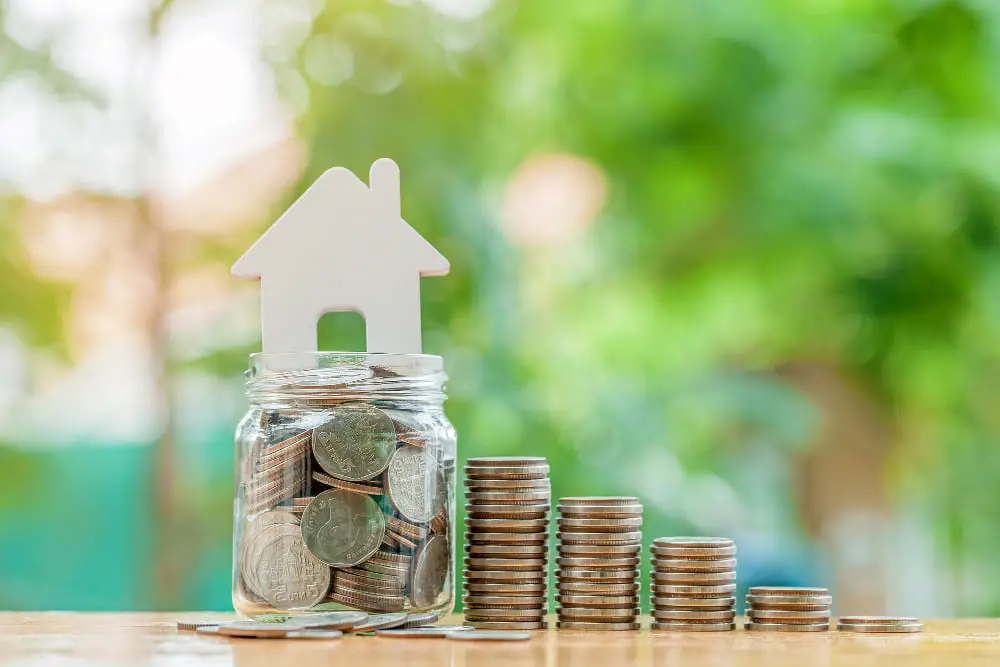
Securing the best deal on a metal building is easier with a few strategies. Firstly, consider ordering your building in the winter months when suppliers may have more flexible pricing. Secondly, if possible, assemble the building yourself to save on construction labor expenses. For this, pre-engineered metal building kits could be a beneficial choice.
Another method is to stick to standard sizes and designs as customization can increase the overall cost. Also, thoroughly research suppliers and choose a reputable one offering high-quality materials at reasonable prices. Last but not least, ensure that you have a clear understanding of what’s included in the quoted price to avoid hidden costs. This could include delivery fees, erection expenses or unforeseen site work. A bit of planning can result in significant savings.
Common Mistakes to Avoid When Buying a Kit Building
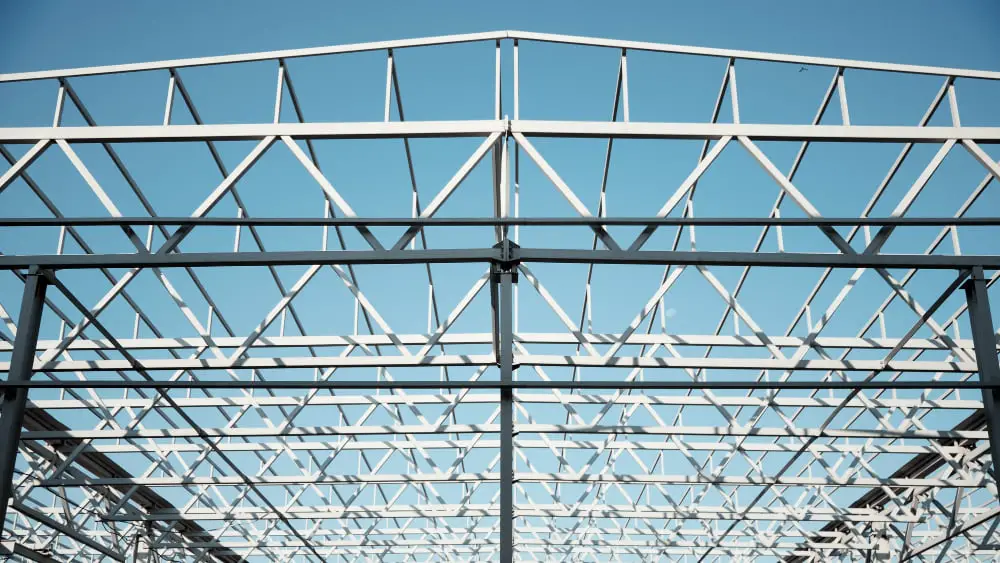
Overlooking local building codes and regulations can be a costly mistake. Always ensure your project adheres to regional codes.
Not considering the purpose of the building can lead to incorrect design choices. Whether it’s for storage, commercial use, or a residence, the use case should guide the building’s design specifications.
Skipping the foundation stage to save cost can risk the building’s structural integrity. Even if it’s a simple structure, the foundation is critical to providing stability and durability.
Neglecting insulation can lead to energy wastage and increased costs in controlling the internal temperature. Look for a kit that includes insulated panels.
Ignoring the manufacturer’s warranty is another mistake. It’s essential to note the terms, coverage, and validity of the warranty for your building.
Choosing the wrong size can be one of the most costly errors. Make sure your chosen size fits both your current and anticipated needs.
Misjudging accessories can also inflate costs. Only choose additions that are necessary for your building. An excess of bells and whistles can derail your budget and timeline.
Remember, each kit building is unique. The nuances of buying and constructing one can vary based on many different factors. Avoiding these common mistakes can help ensure that your project stays on track, within budget, and meets all your requirements.
Steel Building Prices and Comparison
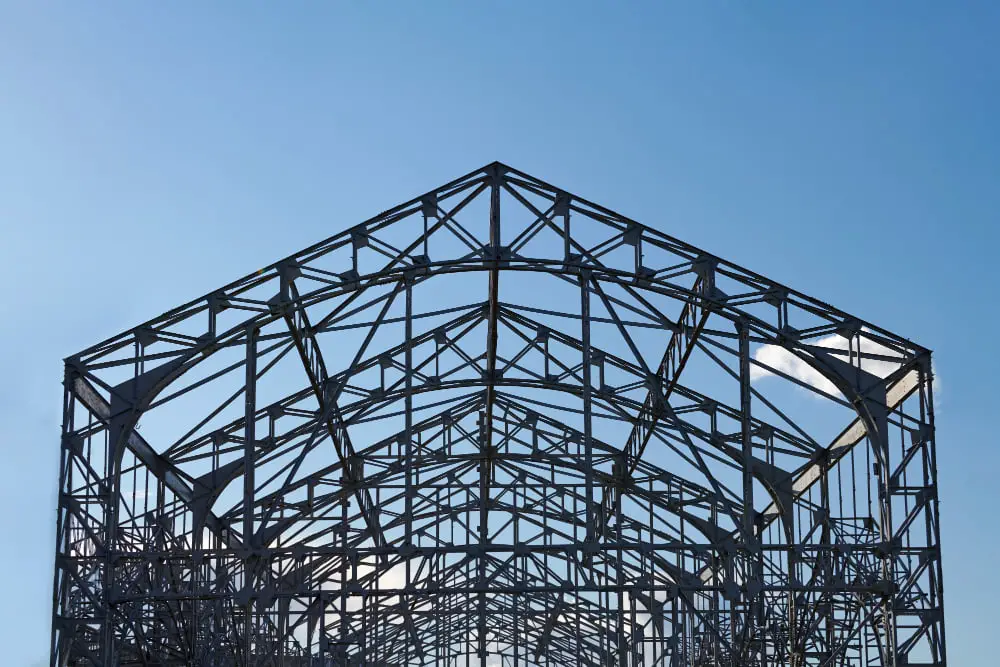
When comparing prices, it’s critical to consider factors such as the complexity of the design, the size of the structure, and the type of steel used. In general, larger and more intricate buildings cost more than smaller, simpler structures. Common steel types include light gauge steel, structural steel, and steel framing, each with different price considerations.
Light gauge steel is economical, readily available, and suitable for smaller constructions. Alternatively, structural steel, although more expensive, offers robust strength perfect for large-scale constructions. Lastly, steel framing is the middle ground regarding cost and strength.
Geographical location also plays a role. Some areas have regulations requiring specific types of steel or building designs, which may impact cost. Likewise, certain regions may have higher delivery and construction costs due to their remote or difficult to reach locations.
Also, bear in mind raw material prices fluctuate, meaning steel costs can vary over time due to market forces, affecting the overall building cost. While obtaining quotations, remember to include all finishing costs, such as insulation and interior work, for an accurate price comparison.
Price Considerations With Metal Building Options
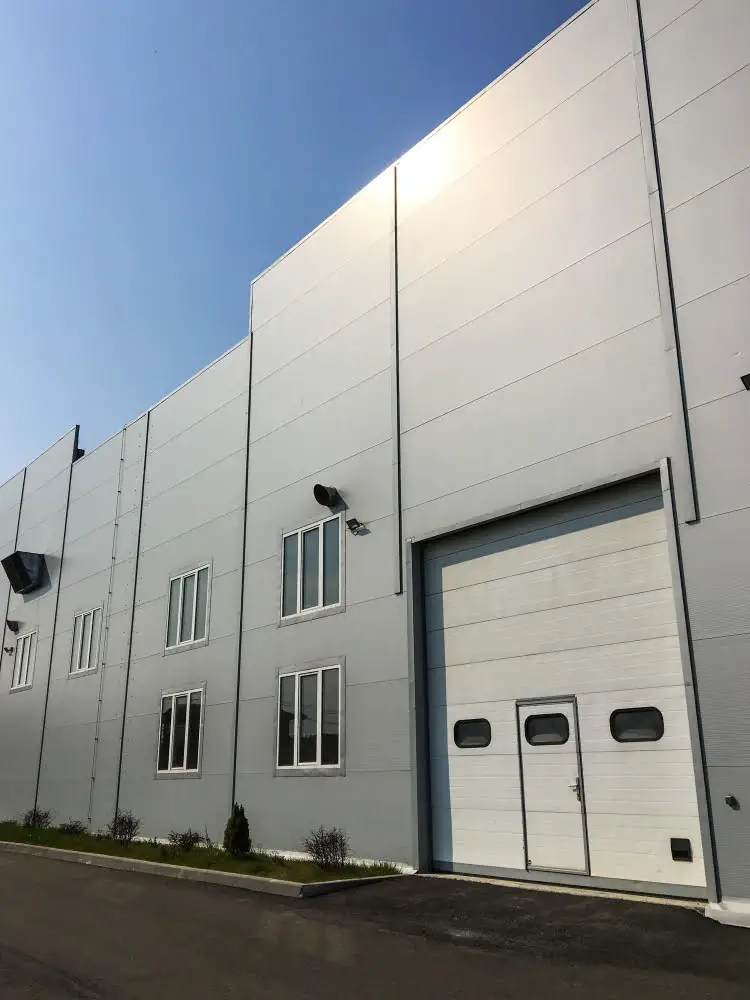
To fully comprehend the pricing dynamics, it’s vital to ponder on the range of options available. First, the complexity of the building design significantly influences the final costs. Simple, box-like structures may come at a lower price, but an intricate design with more corners or angles might increase the cost.
Material selection is another key aspect. High-grade steel is comparatively more expensive, but its durability cannot be overemphasized, potentially resulting in cost savings in the long run.
Finishing touches such as insulation, doors, and windows also play a critical role in the total cost. Of course, opting for high-end finishes would subsequently increase the price tag. But be cautioned, scrimping on essential aspects might lead to increased operating costs afterward.
Lastly, remember to factor in optional accessories like roof vents or skylights into your budget. While these are not necessary, they may improve the building’s functionality or aesthetic appeal. Each of these choices reflects a different price, so careful consideration is necessary to balance your budget and intended use.
The Appearance of a Metal Building Estimate
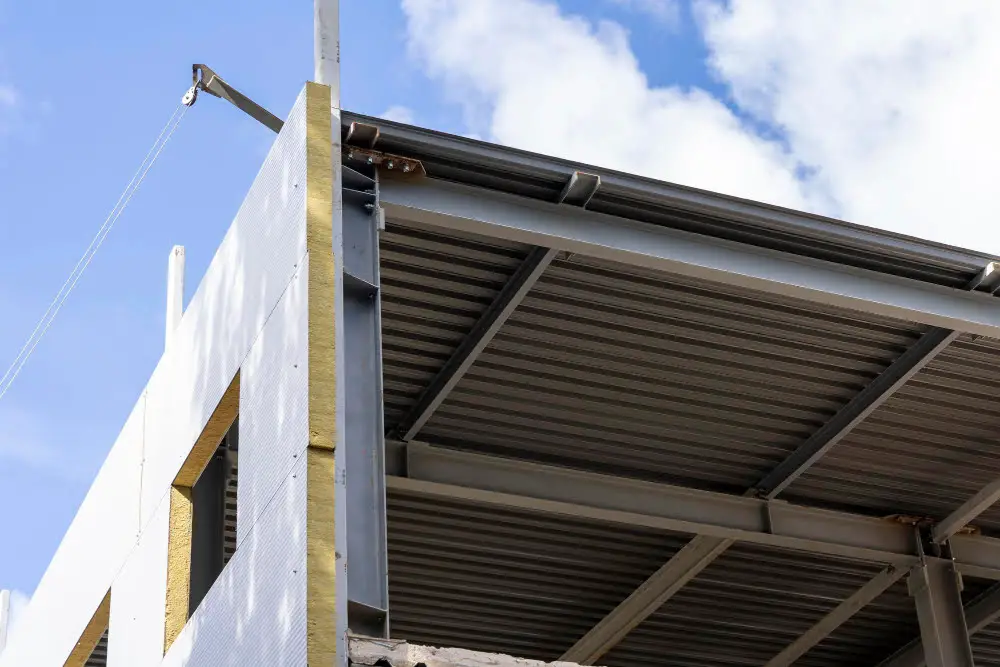
An accurate estimate for a metal building project offers a detailed breakdown of expenses. It typically includes the raw material costs, which largely depends on the size and thickness of the steel used. Also included are direct labor costs—calculated based on the hours needed for construction—and indirect labor costs, such as project management and supervision.
Additional costs found in an estimate might cover the design and customization of the building, from architectural drawings for complex structures to minor adjustments for a more straightforward design. Freight charges can also play a significant part, varying on factors such as distance to site and fuel prices.
Remember, specific additions like gutter systems, insulation, or specialized doors can be extra line items in your estimate. Always check all inclusions and exclusions to avoid any surprises down the line. Match your estimate against your budget, ensuring you get what you pay for, and making adjustments as necessary for a cost-effective project. Contest any unclear items with your supplier before proceeding.
Steel Building Regulations and Their Impact On Price
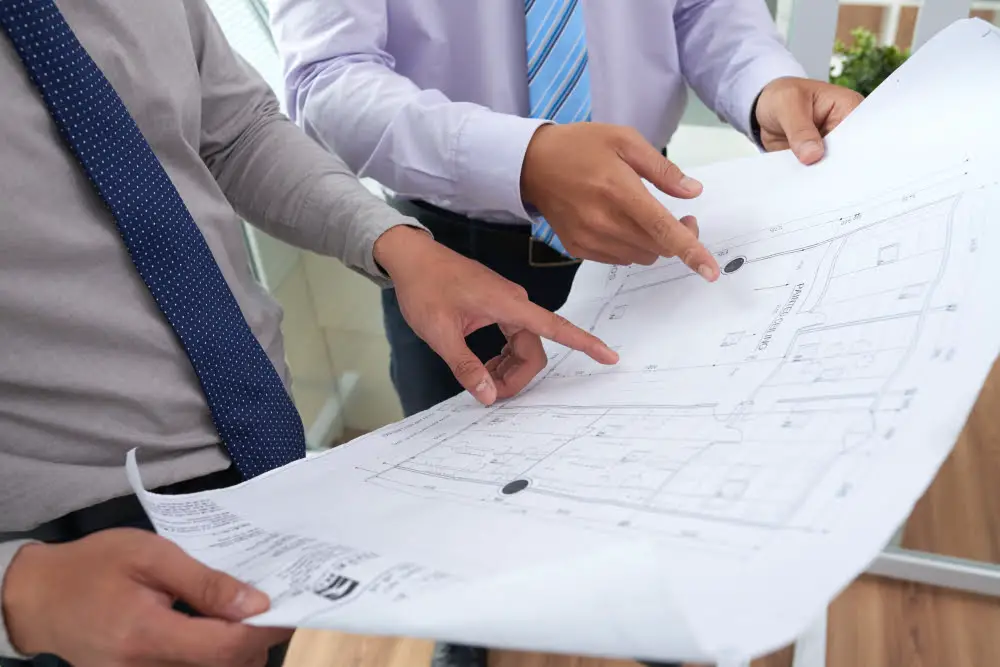
Many factors intertwine to determine the final cost of your steel building project. Of these, building regulations remain a critical aspect. These rules, enforceable by local, state, and national authorities, aim to ensure safe and sustainable construction practices.
Specific requirements can affect your project costs. They include:
- Zoning Laws: Local ordinances dictate where specific types of buildings can be erected. Depending on your proposed site, adjustments might be needed to comply, potentially raising costs.
- Building Codes: Depending on the building’s intended use, certain construction standards must be met, affecting materials used and overall design.
- Environmental Regulations: These include energy efficiency, storm-water runoff, and pollution reduction. Factoring in these requirements can impact both construction and operation costs.
- Fire Safety Regulations: Particularly important in commercial buildings, these regulations determine the type of fire-resistant materials needed, influencing costs.
- Accessibility Standards: Commercial and public buildings must comply with mobility impaired accessibility standards, which could require additional investment.
Each of these plays a significant role in influencing the final cost. It’s crucial to familiarize yourself with the relevant regulations before embarking on your project. Not only will this help keep the project on the right side of the law but also prevent unforeseen expenses that could inflate your budget. Keep in mind that an experienced contractor can guide you through local regulations. This knowledge can help create a smoother, more predictable building process.
Impact of Geography and Weather On Metal Building Prices
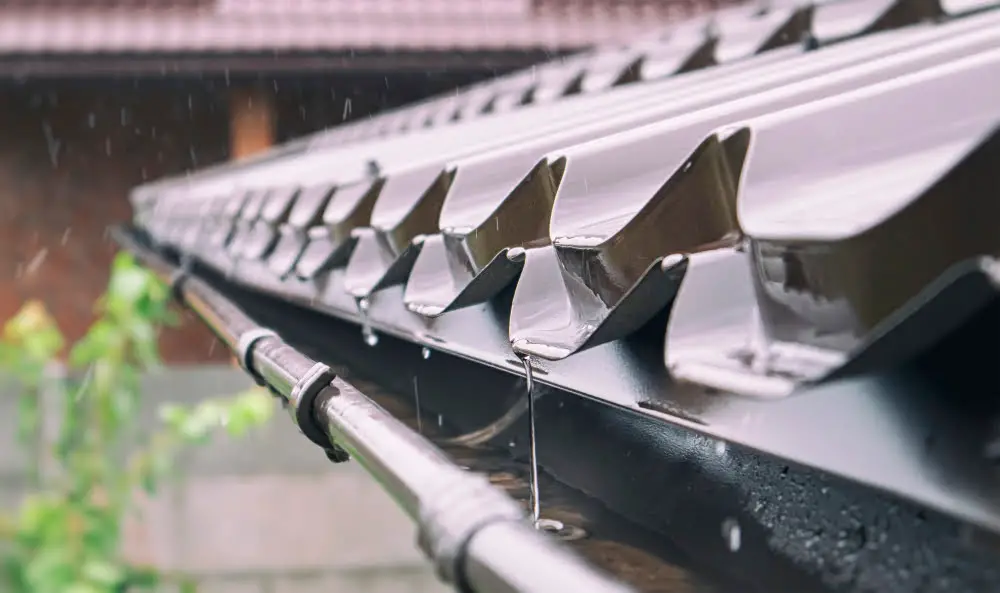
Different geographic locations come with distinct building code requirements that can alter the cost of your metal building. For instance, if you’re in an area prone to high winds or earthquakes, your building might need added structural reinforcements, which will raise the price.
Weather also plays a crucial role in the construction process. Areas with harsh winter conditions may need ground heaters for concrete curing. Rainy regions require careful scheduling to avoid construction delays, while hot climates might necessitate early morning work shifts to beat the heat. Each of these factors can influence labor costs and construction timelines, subtly affecting the overall budget of the metal building project.
Furthermore, the type of soil in your location can impact the foundation type and costs. Rocky or sandy soils may need special construction techniques, such as deep foundations or earthwork, adding to the total cost.
Remember, thorough site analysis and understanding of local building codes can go a long way in appropriately estimating the financial implications of geography and weather on your metal building project.
Impact of Supplier Choices On Metal Building Costs
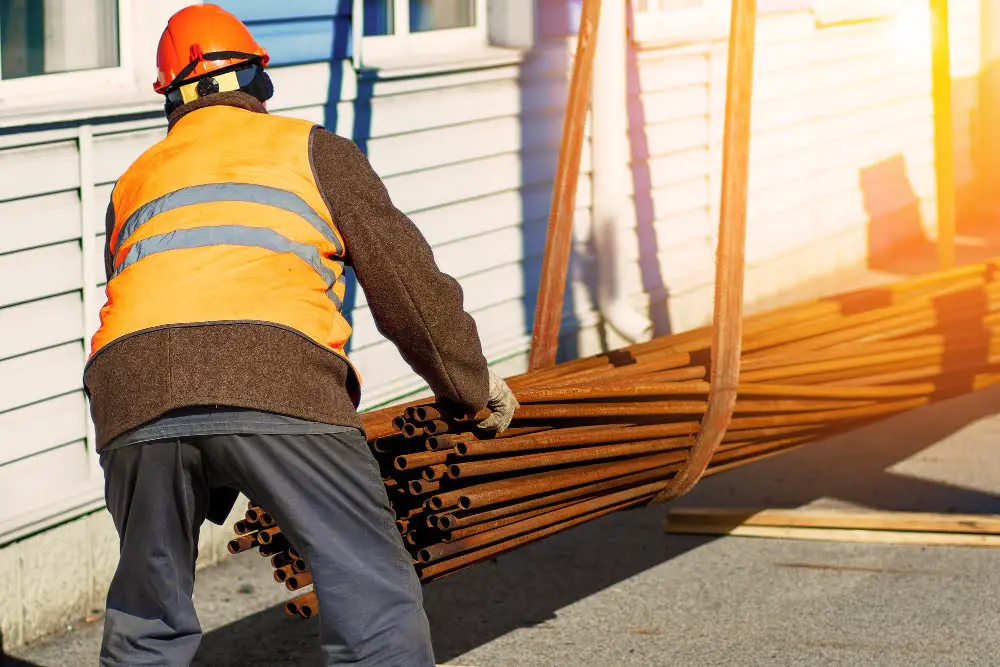
Opting for a trustworthy, established supplier can greatly influence the cost of a metal building project. Firstly, seasoned suppliers have strong relationships with manufacturers, allowing for buying in volume at reduced prices. This cost-saving can be passed to you, lowering your overall project cost.
Second, experienced suppliers offer invaluable guidance on material selection, best practices, and can recommend affordable, quality solutions that newly established suppliers might not be privy to, thus preventing costly mistakes.
Third, suppliers vary in the additional services they provide. Some may offer free delivery, reducing your costs, while others might include free design consultation or installation services in their packages.
Moreover, the supplier’s location matters; if they’re located far from your site, delivery costs might increase, impacting your total bill. Hence, sometimes it might be cost-effective to choose a local supplier instead of an out-of-state one, despite slightly higher material costs.
Lastly, the supplier’s reputation for delivery times and in honoring their warranty should be considered. Delays in delivery could impact your build schedule, thus affecting the project’s cost indirectly. On the other hand, a supplier who promptly honors their warranty can help avoid unwanted repair costs.
Remember, while the initial cost might seem steep with a reputable supplier, the overall value received often outweighs this in the long run. So choose wisely, as the right supplier can have a significant impact on your metal building’s cost.
Cost of Steel and Its Effect On Building Prices
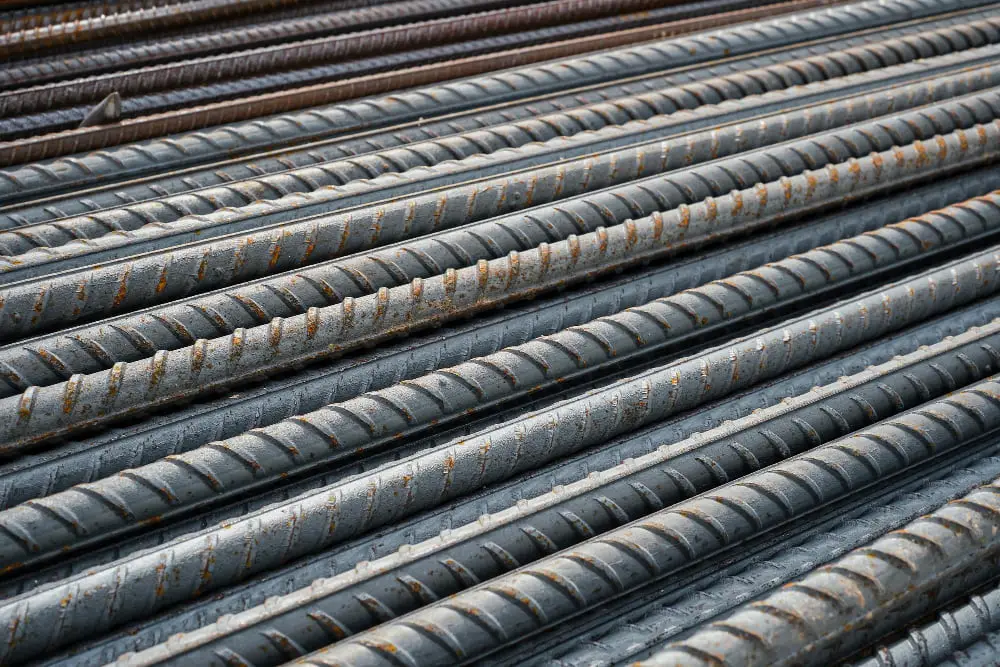
Market fluctuations can significantly influence the cost of steel that is vital for metal buildings. Nationally and globally, steel prices shift based on supply, demand, and international economic circumstances.
1. Raw Material Availability: Steel is produced from iron and carbon. Any shortage or increase in the cost of these raw materials will directly affect the price of steel.
2. Production Process Cost: The cost of labor, energy, transportation, and the technology used in the production of steel can have a substantial effect.
3. Demand and Supply: An increased demand for steel for infrastructure projects can spike steel prices, so can a drop in supply for any reason.
4. Global Economic Factors: Trade policies, tariffs, and international crises can also push steel prices up or down.
5. Recycled Steel: The steel recycling industry can have an indirect influence on steel prices. When recycled steel is abundant and cheap, it can lower the demand for new steel.
All these factors collectively define the steel price at any given time. As a result, the costs involved in the construction of your metal building can be impacted significantly. It’s advisable to stay informed about the current market trends to get the best price possible.
FAQ
Is it cheaper to build your own metal building?
Yes, it is generally cheaper to build your own metal building as steel construction methods are usually half the cost and take half the time compared to traditional construction methods.
Is it cheaper to build a building out of wood or metal?
While the upfront cost of wood buildings could be cheaper, a metal building proves to be more economical in the long run given the lower maintenance costs.
Are metal buildings worth it?
Considering their enhanced durability and minimal maintenance requirements, metal buildings are indeed a worthy investment.
How much does it cost to build a metal building in Texas?
The cost of constructing a metal building in Texas ranges from $5,000 to over $100,000, contingent on the structure’s size and options.
What factors influence the cost of constructing a metal building?
The cost of constructing a metal building is influenced by factors such as the price of raw materials, labor costs, the size and complexity of the structure, and any specialized features or customizations.
How does the cost of metal building construction vary across different states?
The cost of metal building construction varies across different states due to factors such as local building regulations, availability of materials, and labor costs.
What is the estimated cost for the maintenance of a metal building?
The estimated annual maintenance cost for a metal building is approximately 2% to 3% of the initial construction cost.
Recap