Delving into the construction timeline of metal buildings, this article offers insightful facts about the factors influencing their build time.
The duration to construct a metal building depends on a multitude of factors, including the size and complexity of the structure, the efficiency of the construction crew, and the weather conditions.
On average, smaller buildings may take a few weeks to complete, while larger or more complex structures can take several months.
However, it’s important to note that metal buildings are typically faster to erect than their traditional counterparts due to their prefabricated components.
This article will delve into these factors in detail, providing a comprehensive understanding of the timeline involved in constructing a metal building.
Key takeaways:
- Metal building construction time varies based on factors such as size and complexity.
- Metal buildings are faster to erect than traditional buildings.
- Pre-engineered metal buildings offer consistent quality and efficient construction.
- Factors that affect construction time include building size, design complexity, and weather.
- Proper planning, permits, and foundation work are crucial for smooth construction.
Estimating the Steel Building Construction Timetable
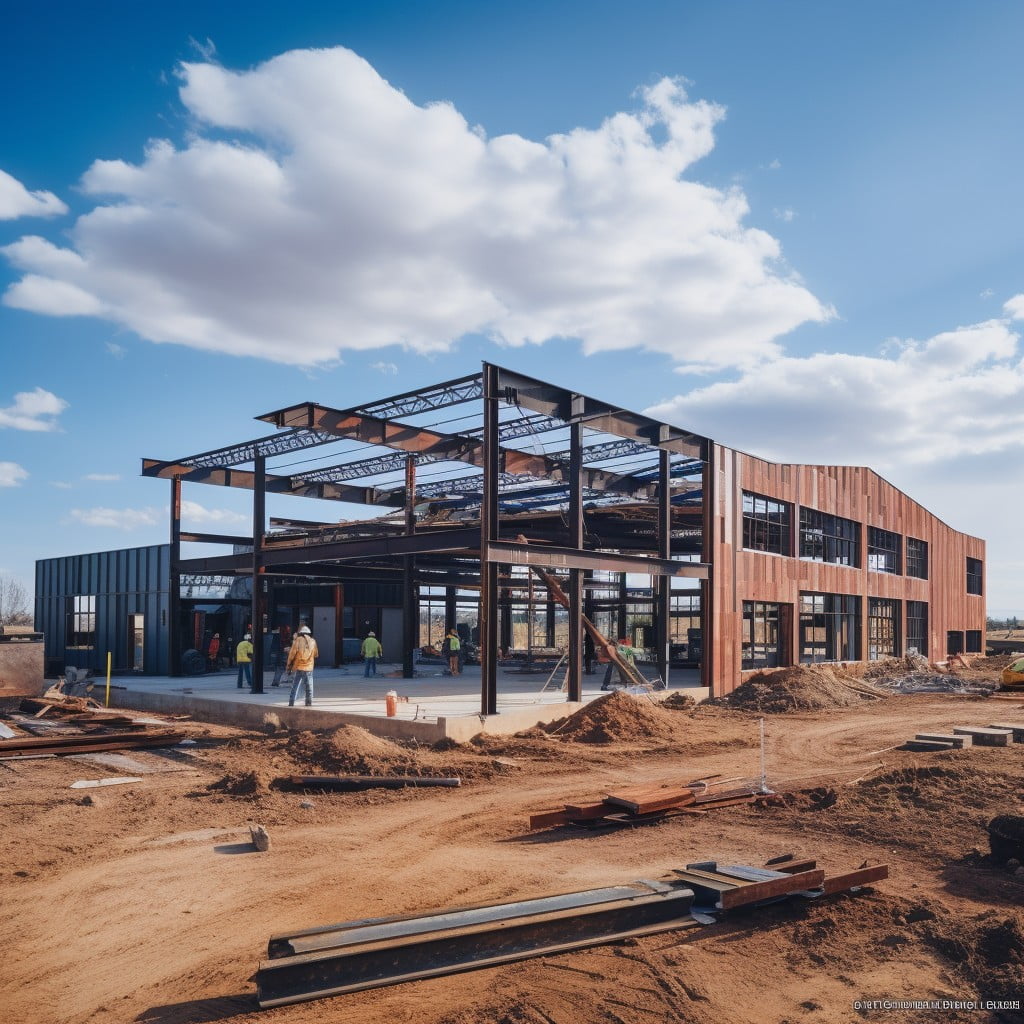
In setting a realistic construction timeline, the scale and complexity of the building design is a key factor. Smaller, simpler structures can be built in as little as six weeks, while larger or more intricate designs require several months, sometimes spanning up to a year. The process includes three main stages – pre-construction which involves planning and permitting, the actual construction, and the finishing touches.
It’s crucial to anticipate possible delays. Difficult site conditions, inclement weather, or a backlog of projects with your builder can prolong the construction phase. While metal buildings are renowned for their quick and efficient build times, keep in mind that customization or complex design features can add to the duration.
Careful planning and working with experienced professionals can significantly streamline the process and keep your project on track. Always plan with a bit of cushion time for unexpected hiccups along the way. Remember, building perfection can’t be rushed.
The PEMB Advantage in Metal Building Construction
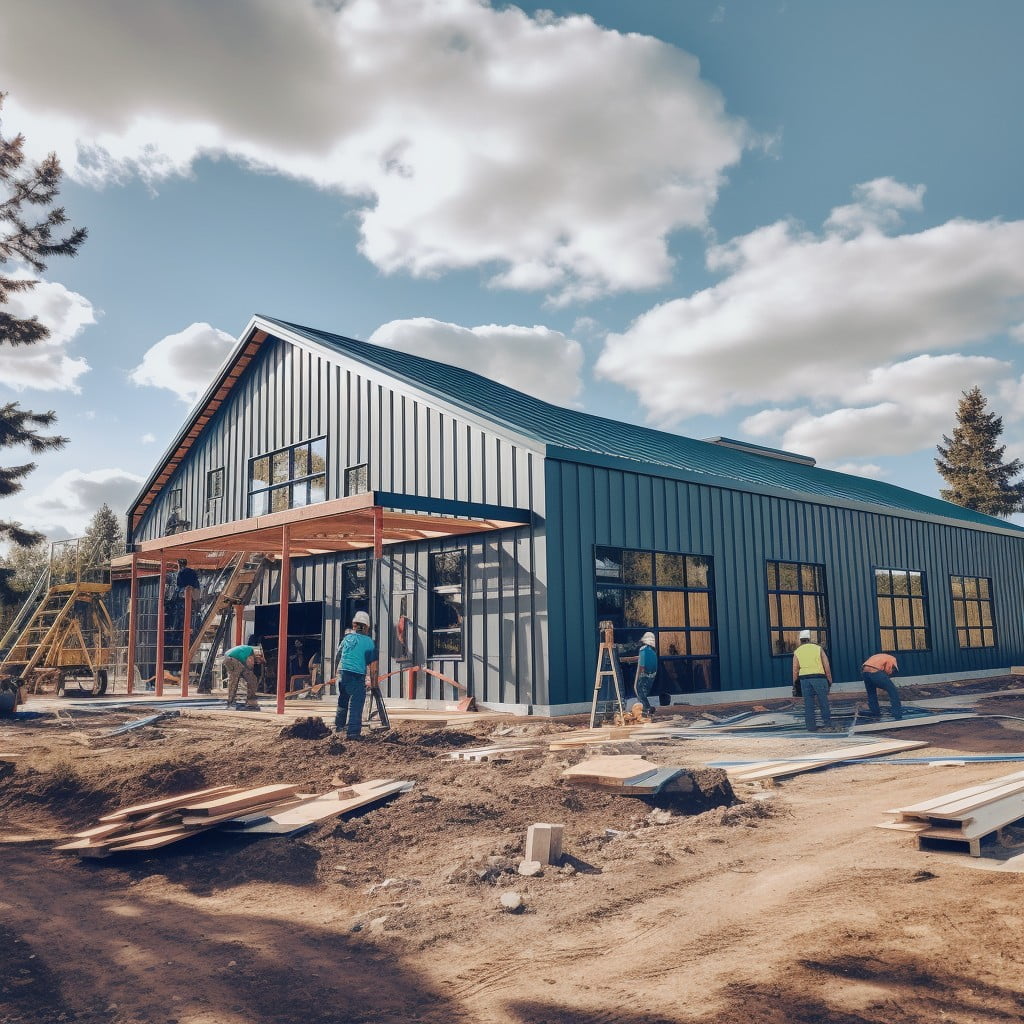
Pre-engineered metal buildings (PEMBs) are a popular choice thanks to their adaptability, durability, and speedier construction process. The pre-fabrication aspect of PEMBs ensures that each component is precision-engineered in a factory, which reduces on-site labor and overall construction time.
To get a better understanding, let’s break down some key points regarding PEMB construction:
1. Consistent Quality: With PEMBs, all the components are designed and manufactured under controlled factory conditions ensuring consistent quality. This eliminates common issues associated with onsite constructions like weather-related delays or inconsistencies in craftsmanship.
2. Efficient Construction: Since all components arrive on site ready for installation, construction time is drastically reduced. It also eliminates the need for on-site fabrications and adjustments.
3. Flexible Design: PEMBs are highly customizable, allowing for a variety of design options to fit your specific needs. It also simplifies and speeds up future expansions.
4. Cost Effective: Thanks to the streamlined manufacturing process, and the reduced need for on-site labor and equipment, PEMBs are typically more cost-effective than traditional buildings.
5. Durability: Steel is known for its strength and longevity. PEMBs, with their steel structure, are highly resistant to harsh weather conditions and are less likely to degrade over time.
Remember, even though PEMBs offer numerous advantages, the actual construction time can greatly vary due to certain external factors including project size, customization requirements, weather conditions, and local building regulations.
Variables That Could Affect Metal Building Construction
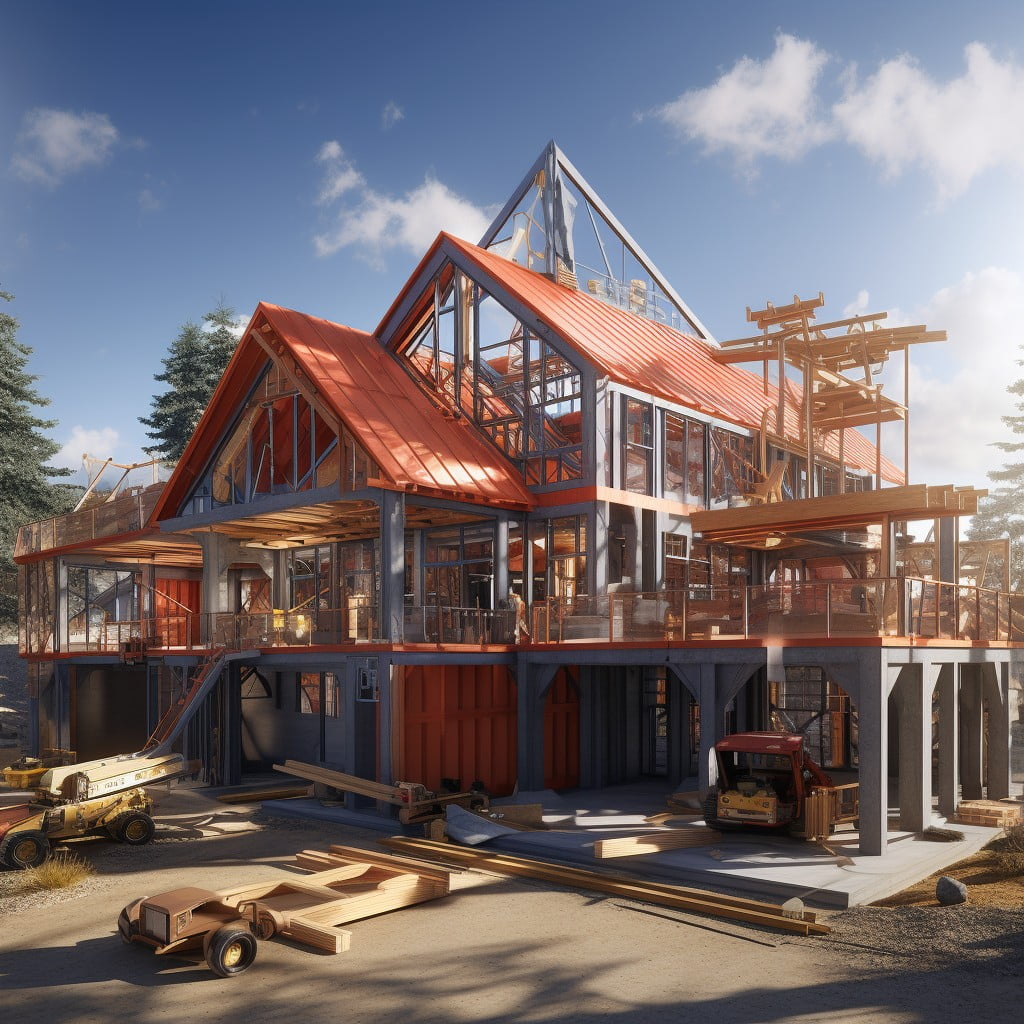
Several elements can impact the duration of a metal building project.
1. Building Size: Larger projects often require a more significant time investment.
2. Design Complexity: Operations with intricate blueprints tend to take longer.
3. Weather: Adverse conditions such as heavy rain or snow can cause delays.
4. Contractor Experience: A seasoned contractor is usually more efficient than an amateur.
5. Site Preparation: If the construction area needs much cleaning, leveling, or soil testing, it can extend the timeline.
6. Required Inspections: Local regulations may necessitate certain inspections that could slow down the process.
7. Special Customizations: Any unique additions like insulation or extraordinary finishes will add some extra time.
Remember, it’s always beneficial to keep these factors in mind when planning the construction timetable.
Acquiring a Building Permit for Your Metal Building
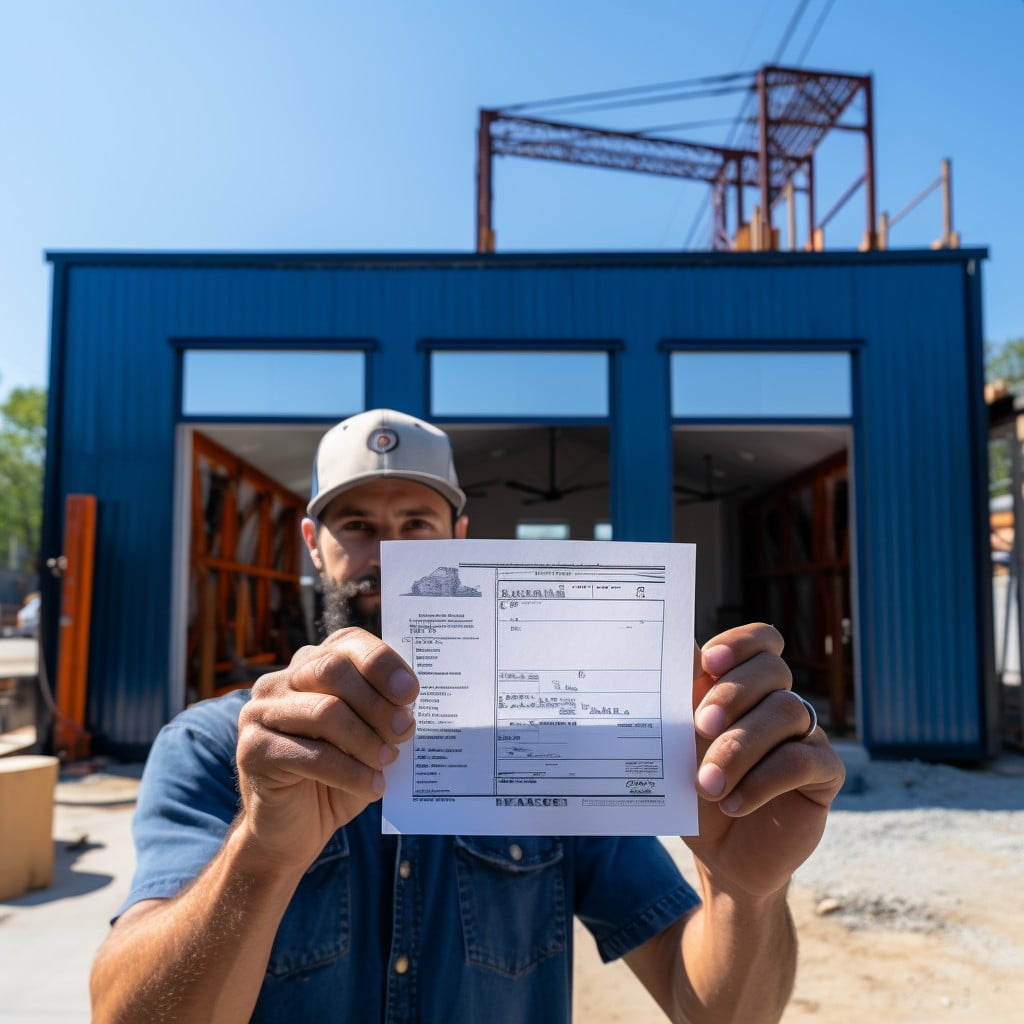
Securing the appropriate permits is undeniably a crucial step in the construction process, as it ensures adherence to local regulations and codes. Structure purpose, size, and location are key elements authorities assess when issuing permits.
In most cases, the process begins with the submission of a site plan, which provides a detailed overview of the proposed construction site. The design or blueprint of your metal building will also be required. Ensure that your plans align with local building codes by consulting a local expert or authority, it may save you from potential delays or costly redesigns later.
Often, you would need to know the soil properties of the construction area, you may need to carry out a geotechnical survey. Bear in mind, it is important to thoroughly complete all required paperwork and pay the necessary fees to avoid unnecessary hitches.
Please note, the duration it takes to obtain permit approvals can vary significantly across different regions ranging from a few weeks to several months. For a smooth process, regulate your schedule to accommodate potential permit delays. This ensures a seamless construction process once you have the green light from regulatory authorities.
Additional Steps: Foundations for Metal Buildings
To effectively anchor a structure, every metal building requires a robust and sturdy foundation. The type of base depends largely on the size of the building and its intended use. For a smaller structure, a simple concrete slab might suffice. However, larger, heavier buildings might necessitate a full basement or a pier and beam setup – a process that may add time to your project’s schedule.
Footings and foundations need proper reinforcement to support the building’s weight and withstand environmental factors such as wind and ground movement. It’s crucial to correctly place rebar in the footing trenches and to treat the concrete properly after it’s poured to maximize its strength and durability.
It’s also vital to moderately dampen the ground if it’s dry before pouring the concrete. This measure reduces the chance of the ground absorbing water from the concrete and homogenizes the concrete’s water content, ultimately ensuring a firm base for your structure.
Another key consideration is the curing period; while concrete might seem dry after a couple of days, it generally takes around 28 days to achieve full strength. Rushing this could lead to issues down the line – a stable and well-cured foundation is worth the wait for your metal building.
Given the intricacies of foundation work, many opt to hire a professional concrete contractor which can increase costs, but ensure a solid base for your metal building construction.
Contracting a Builder for Metal Building Construction
After finalizing the building plan, the next crucial step is to engage the right construction professionals. Although metal building kits are designed for easy assembly, they do require certain skills, especially for large and complex structures.
First, ensure to hire a contractor with metal building experience. This specialist will understand the intricacies of steel constructions, ensuring a smooth assembly process.
Second, remember to clarify all the cost details. The builder’s price can include site preparation, concrete, labor, and sometimes even the structural engineer’s plan review.
It’s also worth noting that reputable metal building manufacturers often have a network of preferred builders. They can recommend a local contractor familiar with their product, which can save you time and hassle.
Finally, check the references for workmanship and reliability. You want to ensure the contractor has a history of projects completed on time and without issues. A background in successfully erecting metal structures will provide an additional layer of assurance.
Delivery Timelines for Metal Buildings
When it comes to the delivery of your metal building components, planning is key. The production process typically takes about six to eight weeks after order confirmation. Understanding this schedule can help in meticulous project planning.
After production, the components are loaded and delivered to the job site. In this regard, consider the following points:
- Clear communication between the supplier and the construction team is vital to ensure timely delivery and subsequent assembly.
- Delivery routes must be thoroughly planned in advance to avoid delays.
- Preparation of the construction site must align with the delivery schedule to ensure immediate assembly upon arrival of components.
Such a systematic approach significantly reduces downtime and allows for a smooth construction process. It is also essential to build in some contingency time for unexpected events, such as adverse weather conditions, which could potentially delay delivery.
FAQ
Is it cheaper to build your own metal building?
Yes, constructing your own metal building can indeed be a cost-effective solution as it often costs half as much and takes half the time as compared to traditional construction methods.
How long does it take to assemble steel frame?
Assembling a steel frame can take a few days for a small structure with a team of four people, and approximately a week for larger structures with a crew of five to seven people.
How hard is it to put up a metal building?
Installing a metal building is generally easier than erecting structures made of other materials, given that they come in prefabricated components engineered to fit together specifically, resulting in a quick and straightforward assembly process.
How thick should a slab be for a metal building?
The recommended thickness for a concrete slab for a metal building is a minimum of 4 inches, with an extra inch added to the perimeter dimensions of the planned building.
What are the essential steps in the construction process of a metal building?
The essential steps in constructing a metal building include preparing the construction site, laying the foundation, erecting the frame, installing the walls and roof, and finalizing with doors, windows, and interior fixtures.
What impacts the duration of a metal building construction?
The duration of a metal building construction is impacted by factors such as the size and design of the building, the complexity of the project, weather conditions, and the experience level of the construction team.
What maintenance is required for a metal building post-construction?
Post-construction maintenance for a metal building typically includes regular inspections for structural integrity, cleaning of the surface to prevent rust, checking and repairing insulation, gutters, and flashings, as well as lubricating doors and windows.
Recap