Learn about FEP polymer, its properties, and how it is utilized in the construction industry to enhance building materials.
Key takeaways:
- FEP polymer is highly resistant to chemicals and corrosion.
- It maintains its properties across a wide temperature range.
- FEP acts as an excellent electrical insulator.
- FEP is transparent, allowing for visual inspection of fluid flow.
- Its low friction surface reduces sticking and snagging.
Fluorinated Ethylene Propylene
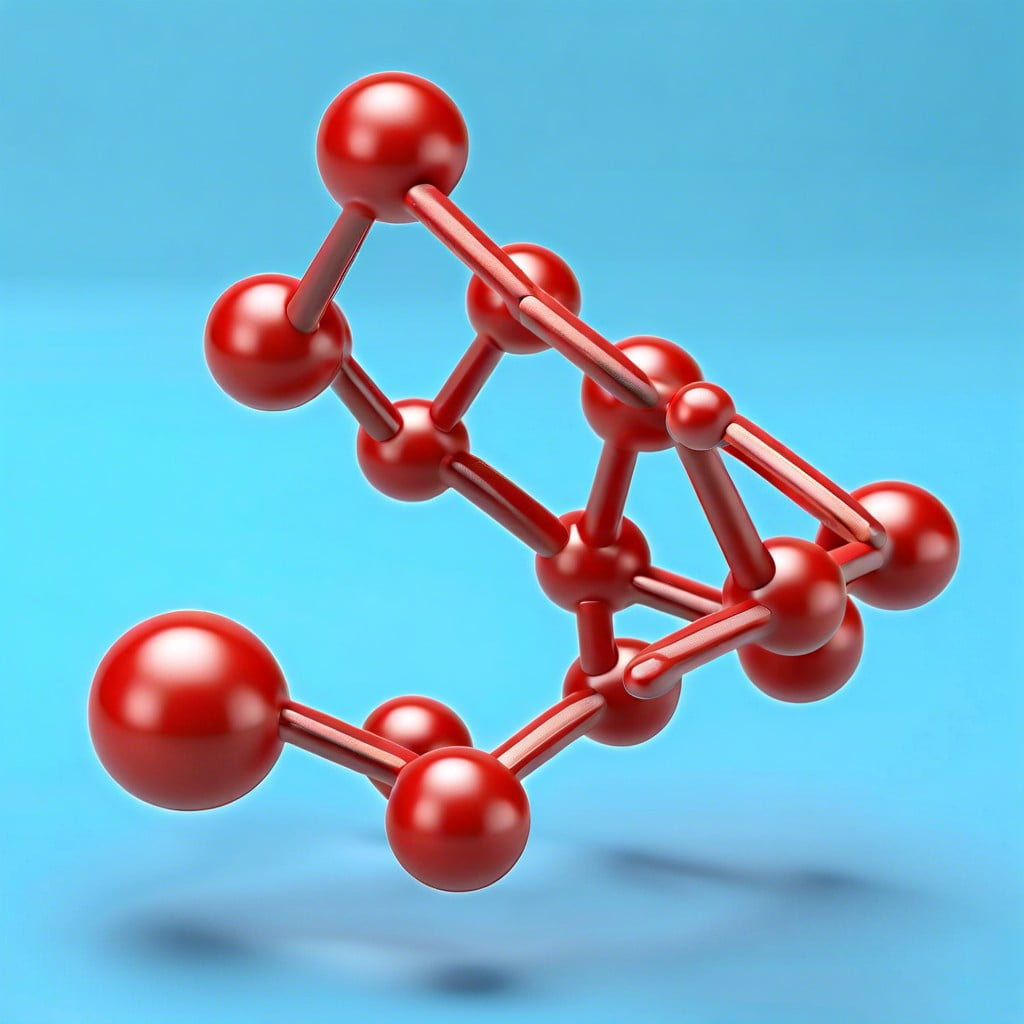
Fluorinated ethylene propylene, more commonly known as FEP, is a robust polymer that belongs to the family of fluoropolymers. FEP shares similarities with PTFE (polytetrafluoroethylene), notably its nonstick properties and resistance to high temperatures. Here are a few key points about FEP:
– **Chemical Resistance**: FEP is highly resistant to a vast spectrum of chemicals, which makes it ideal for use in corrosive environments.
– **Thermal Stability**: With a melting point around 260°C (500°F), FEP maintains its properties across a wide temperature range, ensuring durability and reliability.
– **Electrical Insulation**: It acts as an excellent insulator, and is often used in the cabling and electrical insulation industries due to its low dielectric constant.
– **Transparency**: Unlike other fluoropolymers, FEP is transparent, allowing for visual inspection of fluid flow when used in tubing applications.
– **Low Friction**: Its low friction surface reduces sticking and snagging, which is particularly advantageous in applications involving movement or transport of materials.
Understanding these innate characteristics of FEP provides insight into why this polymer is so valued in construction and various other industries.
Characteristics of FEP
FEP, or Fluorinated Ethylene Propylene, is a robust polymer offering high performance in demanding environments. It is remarkably resistant to chemicals, meaning it doesn’t react with most substances and is an excellent choice for handling corrosive materials. Its non-stick properties are similar to those of Teflon, providing a smooth surface that is easy to clean and maintain.
Noteworthy is the ability of FEP to withstand a wide temperature range, from -200°C to 200°C. This makes it suitable for applications where materials might experience extreme temperatures. Additionally, FEP boasts excellent electrical insulation characteristics, which are essential in construction elements that must prevent electrical conduction.
The material also shows great toughness and flexibility, an advantage when durability and resilience are priorities. Moreover, FEP is UV resistant, ensuring longevity when exposed to sunlight without material degradation.
Transparency is another key feature of FEP. It can transmit ultraviolet and visible wavelengths of light, making it ideal for certain construction applications that require translucency.
Lastly, FEP’s low friction coefficient reduces wear and tear when parts slide against each other, which is vital in moving constructs within buildings.
Applications in Construction
FEP, or Fluorinated Ethylene Propylene, has diverse uses in the construction sector thanks to its remarkable properties. Its resistance to high temperatures and chemical inertness makes it an excellent choice for cable and wire coatings, providing safety and longevity to electrical systems in buildings.
This polymer’s non-stick characteristic and low coefficient of friction are useful in creating easy-to-clean surfaces and components, an asset for spaces requiring high hygiene standards such as hospitals or food processing plants.
Moreover, the translucency of FEP films allows their use in skylights and other architectural features where light transmission is desired, while also offering weather and UV resistance.
FEP’s properties also make it ideal for creating corrosion-resistant seals and gaskets, which are essential in protecting construction materials from harsh environmental conditions and ensuring building durability.
In addition, the material’s flexibility and toughness contribute to innovative uses in construction, such as in the fabrication of flexible and lightweight structures. This allows for creative architectural designs without compromising on material performance.
Overall, FEP’s unique features provide significant advantages in constructing safer, more efficient, and longer-lasting buildings.
Safety and Environmental Considerations
Fluorinated Ethylene Propylene (FEP) is generally considered to be a non-toxic and non-reactive material. It resists combustion and does not emit harmful gases when exposed to flame, which makes it a safe choice for various building applications. However, it is important to recognize that during its manufacture, handling of raw materials requires care due to their toxicological properties.
For environmental considerations, FEP stands out due to its long service life and resistance to aggressive chemicals, which can reduce the need for frequent replacements and maintenance. This durability contributes to less waste and a lower environmental footprint over time. Additionally, at the end of its lifespan, it’s important to dispose of FEP in accordance with local regulations as it is not biodegradable.
In terms of energy efficiency, FEP’s excellent thermal insulation properties can contribute to reducing energy consumption in buildings. Its ability to withstand UV radiation also means that it doesn’t degrade easily when exposed to sunlight, maintaining its performance without requiring energy-intensive maintenance.
While FEP is an incredibly stable polymer, it’s important to ensure that its disposal or recycling is managed properly to prevent any potential release of fluorinated compounds into the environment. The recycling of FEP can be challenging due to its high melting point and the need for specialized facilities to process the material. Research is ongoing to develop more sustainable practices for the end-of-life stage of FEP products.
By handling FEP responsibly throughout its lifecycle, the construction industry can leverage its advantages while mitigating environmental impact.
Emerging Trends and Future Developments in FEP Technology
In the realm of FEP technology, innovation is constant, aiming to enhance performance and widen its application scope. One promising direction is the development of FEP composites with added functionality. These composites may incorporate materials like carbon nanotubes or graphene, substantially improving electrical conductivity and mechanical strength. This augmentation could pave the way for FEP’s deployment in advanced electrical systems within buildings or in constructing energy-efficient smart facades.
Another trend is the eco-conscious evolution of FEP production methods. Breakthroughs in green chemistry aim to reduce the environmental footprint of FEP by optimizing manufacturing processes to minimize waste and energy consumption. Such advances are critical in meeting the construction industry’s sustainability goals without compromising material performance.
The 3D printing revolution is also knocking on FEP’s door. Researchers are experimenting with FEP in 3D printing filaments, which would allow for the creation of complex, bespoke components for specialized construction needs. This could significantly reduce material wastage and enable the production of parts with intricate designs that are difficult or impossible to make with traditional methods.
Lastly, FEP’s role in energy efficiency is gaining traction, with studies exploring its potential in solar panel encapsulation. Its excellent transparency and resistance to weathering make it a prime candidate to protect solar cells, potentially increasing the lifespan and efficiency of solar energy systems. As the world shifts towards renewable energy, FEP could become a staple in constructing eco-friendly buildings.
Recap