Discover how carbon fiber reinforced polymer is transforming the construction industry with its exceptional strength and versatility.
Key takeaways:
- CFRP offers high strength-to-weight ratio for lightweight applications.
- It is corrosion-resistant and maintains shape under stress.
- Low thermal expansion ensures dimensional stability.
- CFRP is durable and resistant to fatigue.
- Challenges in disposal and recycling require specialized processes.
Properties of Carbon Fiber Reinforced Polymer (CFRP)
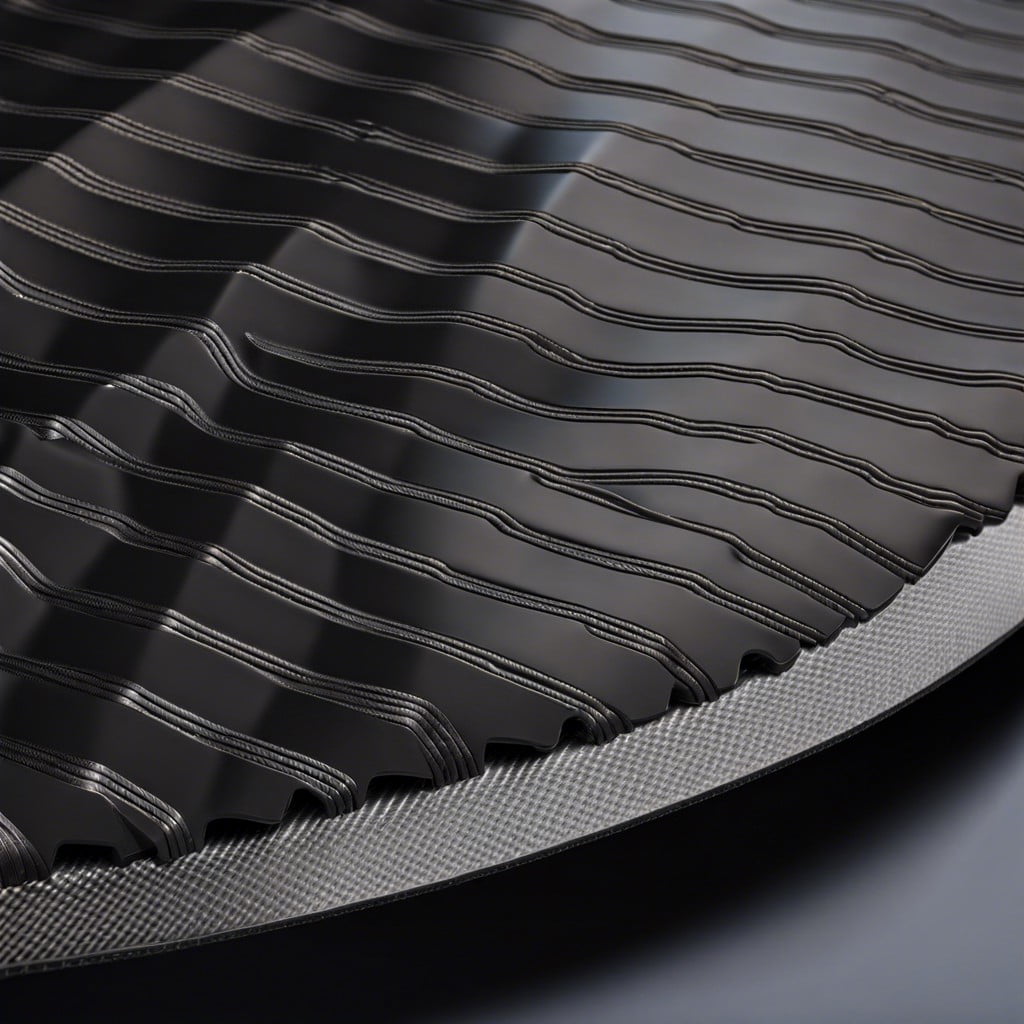
Combining carbon fibers with a polymer resin results in a composite material known as carbon fiber reinforced polymer. This concoction offers several benefits, such as:
High strength-to-weight ratio: CFRP is renowned for its outstanding strength without adding significant weight, making it ideal for applications where lightness is critical.
Corrosion resistance: The material doesn’t rust or corrode, which prolongs its lifespan and reduces maintenance when exposed to harsh environments.
Stiffness: Carbon fiber provides rigidity, which means CFRP components maintain their shape under stress and load, contributing to the stability of the structures they are used in.
Thermal expansion: CFRP has a low coefficient of thermal expansion. This means that it does not expand or contract much with temperature changes, ensuring dimensional stability.
Durability: The material resists fatigue and can handle repeated stress without significant wear, translating into long-lasting components.
The unique combination of these properties make CFRP a preferred material in many technically demanding applications.
Manufacture of CFRP
Carbon fiber reinforced polymer is crafted by weaving carbon fibers into a matrix, typically made of epoxy resin. This braid-like construction optimizes the strength and rigidity of the materials while keeping them lightweight.
The process begins with carbon fiber production, involving the carbonization of materials like PAN (polyacrylonitrile), pitch, or rayon at high temperatures. Once obtained, these fibers are then aligned, woven or layered into sheets, or onto a mold, according to the desired shape and mechanical properties.
The next step involves impregnating the fibers with a resin mixture. Carefully controlled resin infusion methods ensure that the resin spreads uniformly, bonding with the carbon fibers. Vacuum bagging and autoclave curing are common techniques used to achieve high-quality consolidation and to remove any air pockets that might weaken the material.
After curing, the composite takes on its final form—hardened, resilient, yet impressively light. The result is a material that boasts superior tensile strength, stiffness, and temperature tolerance, making it a prime choice for high-performance applications.
Applications of CFRP
Carbon fiber reinforced polymer is prized in construction for its strength-to-weight ratio, leading to its use in high-performance structures. In bridges, CFRP can be found in cables, rods, and reinforcing plates, contributing to light, durable, and long-lasting designs. It also serves in strengthening applications, where it is bonded to existing structures, enhancing their load-bearing capacities without excessive weight.
In commercial and residential buildings, architects harness CFRP’s versatility for striking facades or as a supportive, non-intrusive retrofit material. It’s particularly useful in earthquake-prone areas, where its flexibility and strength help absorb seismic forces.
Beyond buildings, CFRP extends to infrastructure projects like water treatment plants, where its resistance to corrosion means a longer life for tanks and pipes exposed to aggressive chemical environments. In all these applications, carbon fiber reinforced polymer brings resilience, longevity, and a futuristic edge to modern construction projects.
Disadvantages of Carbon Fiber Reinforced Polymer
Despite the impressive strength and lightweight nature of carbon fiber reinforced polymer, there are several drawbacks to its use.
Firstly, CFRP materials are often expensive. The cost stems from both the materials itself, such as the carbon fiber, and the manufacturing processes, which can be labor-intensive and require specialized equipment.
Secondly, CFRP has a limited shelf life. The epoxy matrix used in their composition might degrade over time, especially when exposed to sunlight or chemicals, reducing the material’s overall lifespan.
Additionally, the impact resistance of CFRP is lower compared to metals. While it’s strong when it comes to tensile stress, it can be more susceptible to damage under a sharp impact, which can lead to delamination or cracking.
Another issue is the difficulty in repairing CFRP structures. Repair of these materials usually requires specialized knowledge and equipment, making it not only challenging but also costly.
Lastly, carbon fiber’s conductive nature can be a double-edged sword. While useful in some applications, it can also lead to galvanic corrosion when in contact with certain metals, which requires careful design consideration to prevent.
These factors, while not detracting from the many benefits of CFRP in construction, must be carefully weighed during the material selection process.
Disposal and Recycling of CFRP
The long lifespan of carbon fiber reinforced polymer is a plus, but what happens at the end of that life? Disposal and recycling pose significant challenges due to the material’s resilience and the binding matrix that holds the carbon fibers together. Traditional recycling methods, like melting, don’t work because the high temperatures required to break down the polymer matrix can damage the carbon fibers, stripping them of their valuable properties.
To overcome this, specialized processes are necessary. Chemical recycling is one such method, where solvents or chemicals break down the polymer matrix, freeing the carbon fibers for reuse. Another method is mechanical grinding, where CFRP is ground into small particles that can be used as fillers in new composite materials, though this often compromises the strength of the original fibers.
Thermal decomposition offers another approach. This method heats CFRP in a controlled environment to degrade the polymer matrix and recover the fibers, although this can be energy-intensive and may impact the quality of the recovered carbon fibers.
Researchers are also exploring more environmentally friendly options, such as using enzymes and bacteria to degrade the polymers without harming the fibers. These innovative methods can open up new possibilities for fully recycling CFRP in the future.
Effective end-of-life management for CFRP helps mitigate environmental concerns and can turn waste into valuable resources, underlining the importance of focused research and development in this domain for a more sustainable future.
Recap