This guide provides a comprehensive understanding of ABS Polymer, its properties and its usage in the construction industry.
Key takeaways:
- ABS stands for Acrylonitrile Butadiene Styrene.
- ABS has a balance of durability, heat resistance, chemical resistance, electrical insulation, and surface finish.
- ABS is used in a wide range of products, including protective gear, kitchen appliances, electronic housings, and toys.
- ABS has limitations such as susceptibility to UV degradation, low melting point, potential for cracking under stress, and non-biodegradability.
- ABS is commonly used in construction for piping, wall paneling, decorative trim, electrical housings, safety helmets, and tool components.
ABS – What Does It Stand For?
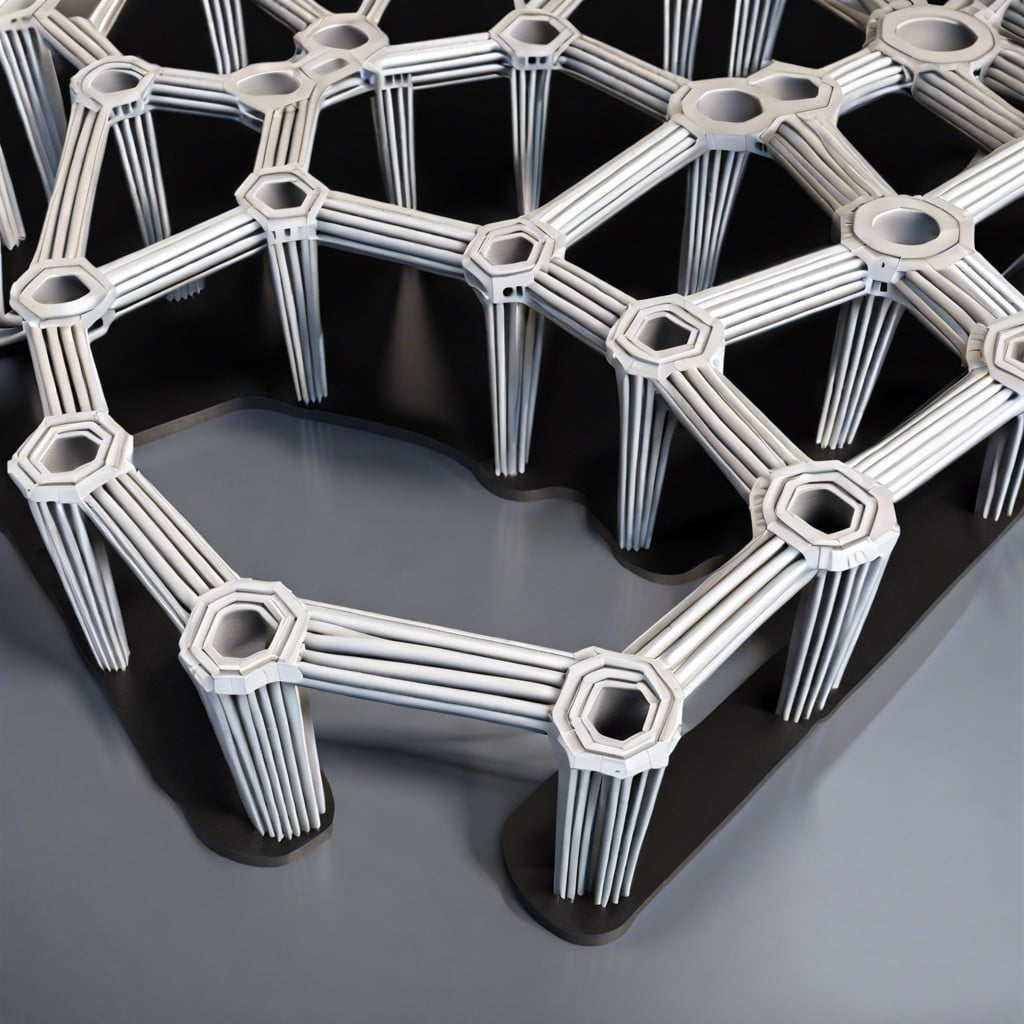
ABS is an acronym for Acrylonitrile Butadiene Styrene, a thermoplastic polymer. It is composed of three distinct monomers:
- Acrylonitrile contributes to the polymer’s chemical resistance and stiffness.
- Butadiene enhances its toughness and impact strength.
- Styrene affords the finished material a glossy finish and improves its processability.
This unique blend of components leads to a versatile material with a balance of useful features. ABS can be injection molded, extruded or thermoformed, making it a popular choice in various industries.
Key Properties of ABS
Acrylonitrile Butadiene Styrene (ABS) is a thermoplastic polymer known for its unique blend of properties which make it widely useful:
- Durability: ABS is tough and shows a good balance of tensile strength and rigidity, which allows it to withstand heavy use and minor impacts.
- Heat Resistance: It can tolerate temperatures as high as 80 to 100 degrees Celsius before deforming, making it suitable for applications where heat is a factor.
- Chemical Resistance: This polymer resists many acids, alkalis, and oils, which is beneficial for products that might be exposed to harsh substances.
- Electrical Insulation: ABS has good insulating properties, meaning it can be used in various electrical and electronic housings.
- Surface Finish: The material has a pleasant glossy finish that can be easily painted or glued, providing versatility in design and appearance.
- Machinability: It can be easily machined, sanded, or turned, which makes the manufacturing process versatile and efficient.
These physical and mechanical characteristics make ABS an adaptable material for a range of construction and manufacturing needs.
Benefits of Using ABS in Manufactured Products
Constructed with a balance of desirable attributes, ABS is a go-to material for a range of products. Its robustness allows for impact resistance, crucial for items that must endure wear and tear, such as protective gear and toys.
Thermal stability ensures that products can withstand varying temperatures without deforming, which is essential for automotive components and kitchen appliances.
Furthermore, ABS’s surface smoothness allows for a high-quality finish, with easy painting and glueing properties that enable versatility in design. This plastic not only machines with precision but also allows for energy-efficient production due to its easy processability, from injection molding to extrusion, making it a cost-effective option for mass production.
Lastly, ABS is favored for its good electrical insulation properties, pivotal for electronic housings and gadgets.
Limitations of ABS
Despite its versatility, ABS does have some drawbacks. Its lower resistance to UV light can lead to deterioration if exposed to the sun for extended periods without proper UV-stabilizing additives.
ABS also has a relatively low melting point around 105°C (221°F), which limits its use in high-temperature applications.
Additionally, it can be prone to cracking under stress, particularly when in contact with certain solvents or chemicals.
Environmentally, ABS is not biodegradable; recycling it is preferable, but the recycling rate is currently lower than ideal.
Furthermore, the manufacturing process of ABS involves petrochemicals, which raises concerns about sustainability and environmental impact.
Applications of ABS
In the realm of construction, ABS shows up in a variety of applications, thanks to its strong, yet lightweight characteristics. For example, it is frequently used for piping and fittings, offering a durable alternative that stands up to abrasive materials and resists physical impacts. Builders often select ABS pipes for drainage, waste, and vent systems because they can endure a wide range of temperatures without warping.
Beyond the plumbing, the material finds its way into the fabrication of wall paneling, where its rigidity and aesthetic versatility make it a compelling choice. Not restricted to hidden structural uses, you’ll find ABS in decorative applications such as trim and molding, which can mimic the look of wood or metal.
In the broader scope of construction, ABS is a go-to for electrical and electronic housings, safety helmets, and tool handles, valuing its insulating properties and comfort in use. The versatility of ABS is on full display when it’s molded into intricate components for items like power tools or junction boxes, where precision and reliability are non-negotiable.
FAQ
Is ABS plastic good quality?
Yes, ABS plastic is of good quality due to its high durability, ability to withstand major impacts, adjustable thickness, and protective characteristics.
Is ABS plastic stronger than plastic?
Yes, ABS plastic is stronger and more durable than PVC plastic.
What are the disadvantages of ABS plastic?
The main disadvantages of ABS plastic are its limited outdoor application due to brittleness and discoloration over time, its combustibility, and the potential release of toxic fumes when melted or burned.
Is ABS plastic or rubber?
ABS plastic is not rubber; it is an opaque thermoplastic and amorphous polymer created using a blend of two plastics (acrylonitrile, polystyrene) and one rubber (butadiene).
How does temperature affect the properties of ABS plastic?
Temperature affects the properties of ABS plastic by reducing its strength and stiffness when exposed to high temperatures, making it more susceptible to deformation.
Can ABS plastic be recycled and how does this process work?
Yes, ABS plastic can be recycled through a process that involves shredding the material into small pieces, washing to remove impurities, melting, and then reforming them into new products.
What distinguishes ABS plastic from other types of polymer in terms of its structural properties?
ABS plastic, short for Acrylonitrile Butadiene Styrene, is distinguished from other polymers by its high tensile strength and robustness, excellent impact resistance, even at low temperatures, and its ability to be injection molded and extruded, which make it widely useful in construction applications.
Recap